REFINERIES AND PETROCHEMICAL
Thermax’s cooling solutions deployed in various processes of refineries and petrochemical plants can effectively improve their energy and economic performance. In addition to optimisation of the industry’s energy consumption, our solutions also contribute to significant yield improvement
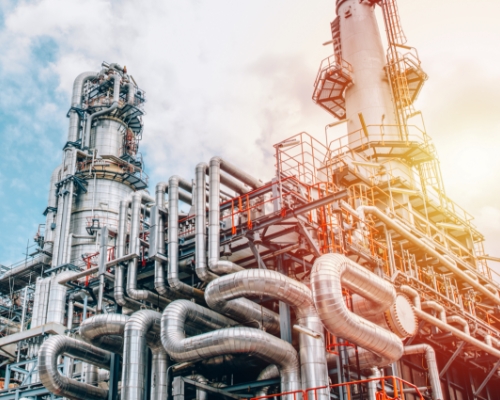
REFINERIES & PETROCHEMICAL
- Mono ethylene glycol (MEG) absorption
- Capacity enhancement of process heat exchangers
- FCCU yield improvement
- DeHazing process
- Effluent treatment
- Gas Separation
MEG ABSORPTION
MEG is formed by reaction between Ethylene Oxide (EO) and water. EO has high affinity towards water and when the EO to water ratio is high, more MEG is produced. Ethylene oxide made inside the EO reactor section must be further enriched to extract more EO. Water is added in the EO scrubber section to enable EO gas absorption. Lower the water temperature better is absorption. The EO in gaseous form (80% EO) is moved to the MEG plant. In the MEG plant, water is added in the section called Re-Absorber. A high EO to water ratio is maintained so as to get a higher yield of MEG in the glycol reaction section. After this, the water is separated out from the products (MEG, DEG, TEG and PEG) in the evaporation section by heating and the steam generated in this section is used in the stripper section. Absoprtion chiller is installed in the Lean water line returning from stripper section to the scrubber section. If the return water temperature is dropped from original 37°C to 34°C, the overall absorption effect increases considerably which is sufficient to increase the plant output to 140%.CAPACITY ENHANCEMENT AND PROCESS HEAT EXCHANGER
During the planned shutdown in refineries, heat exchangers of process condensers are usually found to be affected by heavy fouling and scaling - on the tubes and at the shell as well at the inlet and outlet pipes. Corrosion is an additional issue of concern in the heat exchangers. The corrective cleaning procedure is time consuming and expensive. Hence, it is optimal to reduce the water temperature in the process condenser so that it operates at designed conditions. Absorption chillers are installed to supply chilled water to process condensers @ 28°C. By lowering the process water temperature, designed conditions of the process condensers can be achieved. Installation and piping for the Thermax absoprtion chiller is done without shutting down the plant by “Hot Tapping” process. Thermax absorption chiller is skid mounted so that it can be shifted from one plant to another.FCCU YIELD IMPROVEMENT
Fluid catalytic cracking (FCC) is one of the most important conversion processes in modern petroleum refineries. It is widely used to convert the highboiling, high-molecular weight, hydrocarbon fractions of petroleum crude oils to more valuable gasoline, olefinic gases, and other products. For the recovery of propylene or LPG from hot gases through FCC, cooled naptha is supplied as an absorbent. Conventionally cooling of naptha is done by cooling water because absorption power of naptha increases with lowering the temperature. To enhance the recovery of propylene or LPG, chilled water from absorption chiller can be circulated instead of cooling water.DEHAZING
De-hazing is a process for de-watering distillate fuel oil to render the final product clear and bright. It includes the steps of passing the fuel oil from the stripping step after process heat recovery and prior to sending for storage to a first heat exchanger. Then a separate heat exchange system to sequentially reduce the temperature of the moisture laden oil before introducing the oil to a sand coalescer vessel where removal of the moisture takes place. The feed to coalescer would be pre-cooled by absorption chiller, thereby making most of the water in diesel as un-dissolved and hence could be removed in electrostatic coalscer. Absorption chiller aids the refinery’s coalscer in reducing the moisture content from High Speed Diesel (HSD) and Export Quality Gas Oil (EGO).EFFLUENT TREATMENT
At present, Effluent treatment facility (ETF) of refinery consists of removal of Free or emulsified oil contained in waste water streams and a biological treatment in the aerated lagoon, before it is discharged to the sea. Although each refinery already has dedicated effluent treatment facilities, the accentuated discharge limits of industrial effluent streams by environment authority makes it necessary to improve and extend these facilities. The treatment consists of free or emulsified oil removal (Pre-treatment), sulphide removal, BOD/ COD reduction through biological oxidation and suspended solids removal (Post – treatment). The existing facilities for free oil and emulsified oil removal will be re-used and extended with Chemical Oxygen Demand (COD) degradation, sulphide oxidation, nitrification and filtration steps. The effluent will be treated at refinery site. Free oil removal is accomplished in the existing Corrugated Plate Interceptors (CPI). The oil is sent to the existing wet slop system while the effluent is routed to the DAF (Dissolved Air Flotation) unit for emulsified oil removal. The skimmed oil from the DAF unit is further handled in the existing oily sludge handling systems. The oily effluent is mixed together with the stripped sour water effluent streams and directed to the pre-aeration equalization tanks. Effluent from the equalization tanks will be mixed with spent caustic. The total effluent is cooled before it enters the pre-aeration basins for sulphide oxidation and COD degradation.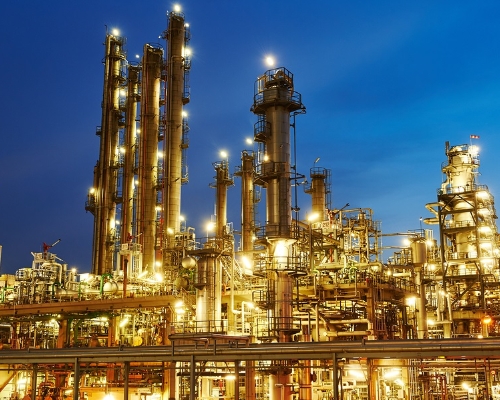
BENEFITS
- Significant yield improvement
- 50% water savings
- Reduced energy consumption
- Electricity-free cooling
- Flexibility to seasonal changes
To know more about the application and benefits of our solutions, contact our experts now
OUR OFFERINGS
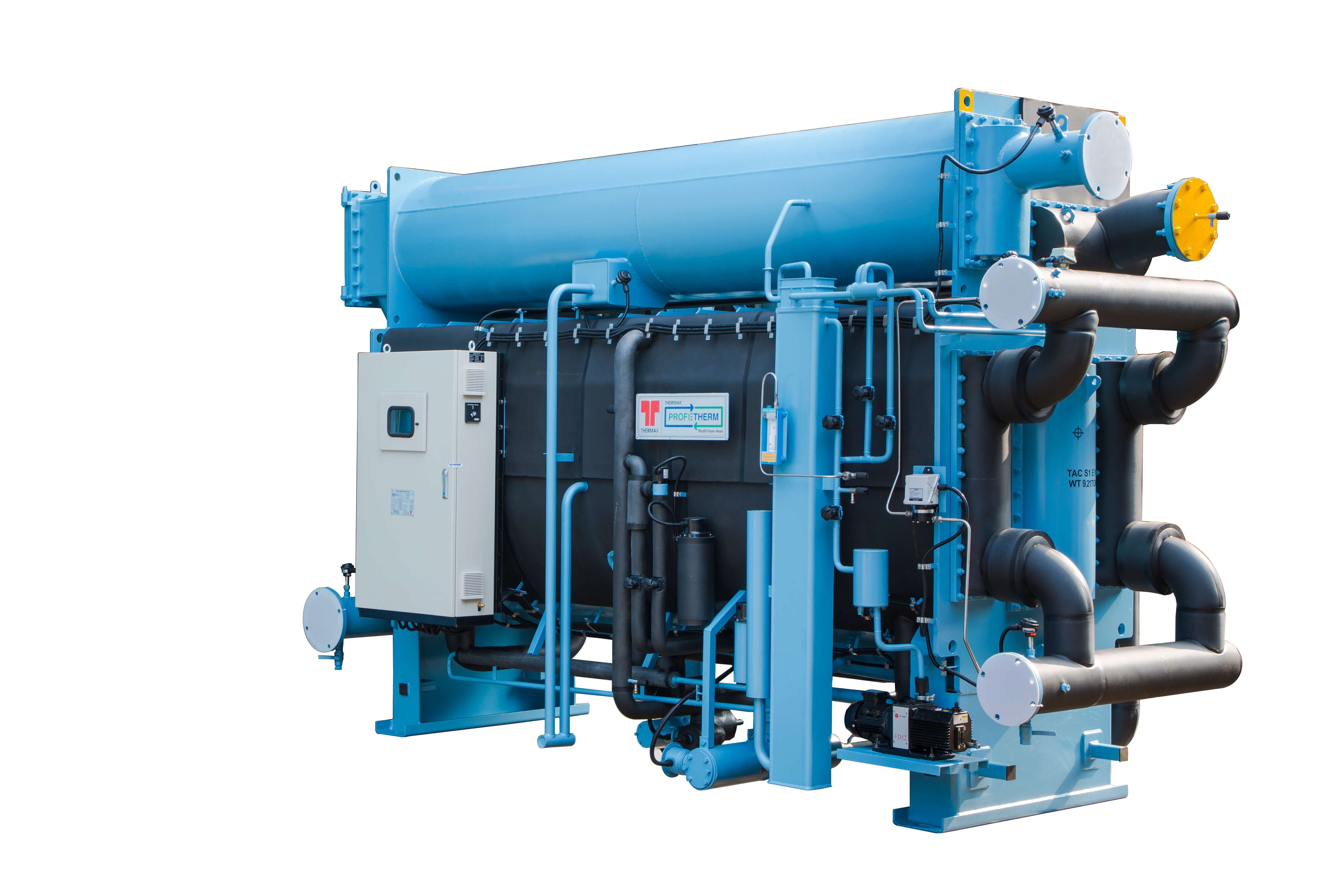
SINGLE EFFECT STEAM DRIVEN VAPOUR ABSORPTION CHILLER
Heat Source: Steam
Pressure: 0 bar.g – 3.5 bar.g
COP: 0.8
Capacity: 100 – 3500 TR
Heat energy available in the form of (LP- low pressure)
- LP vapour (0.1 bar.g, 103OC) coming from continuous polymerisation process in textile industry
- LP steam generated from potato fryer, instant noodle plant etc.
- LP Steam extraction from steam turbine in power plants
- Flash steam recovery
SINGLE EFFECT LOW TEMPERATURE HOT WATER DRIVEN VAPOUR ABSORPTION CHILLER
Heat Source: Hot Water
Inlet water temperature: 80OC – 120OC
COP: 0.8
Capacity: 180 – 1650 TR
Heat energy available in the form of
- Engine jacket water
- Hot water from solar collectors
- Process condensate
- Flue gas recovery from incinerators
- Process heat recovery
- Fuel cells
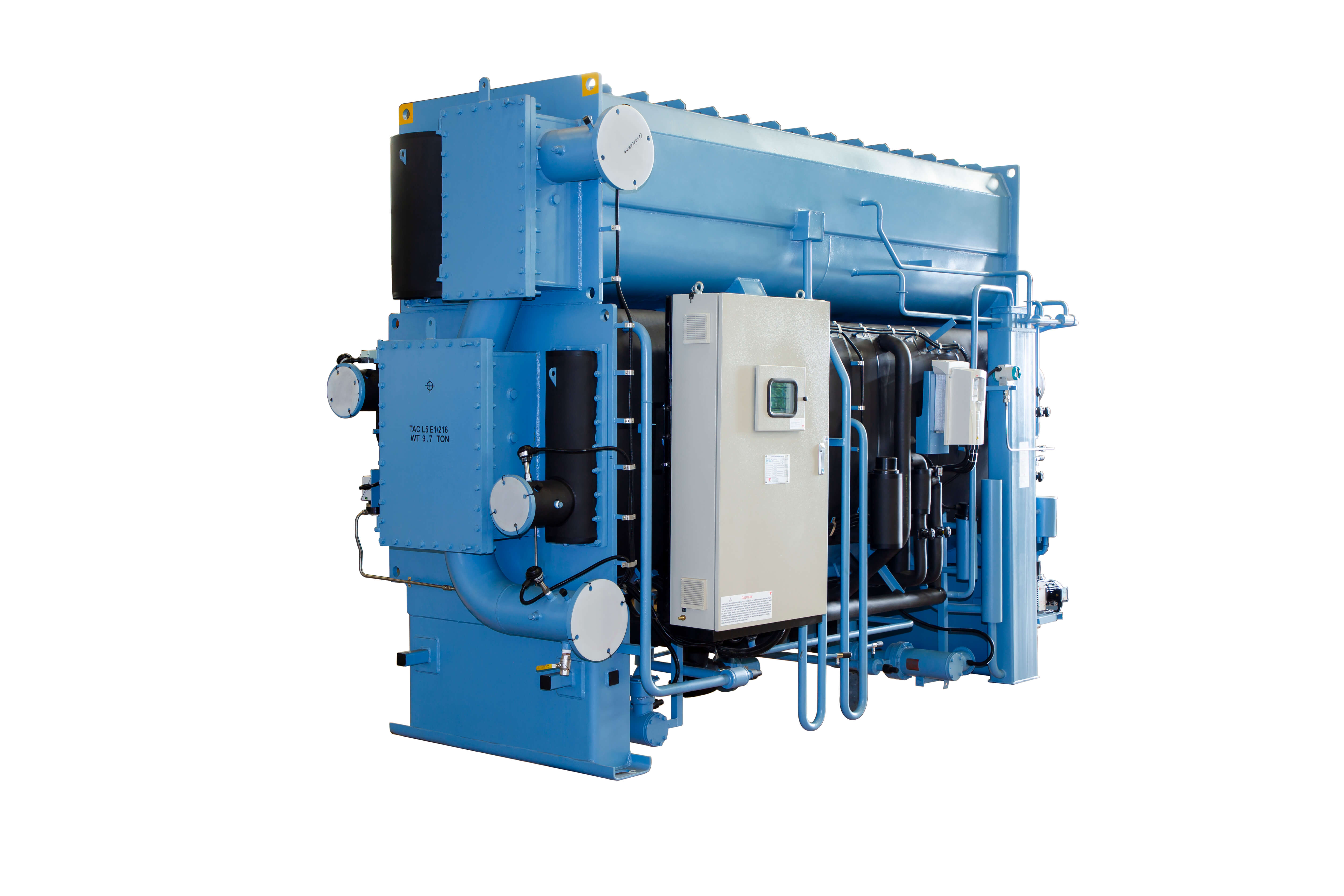
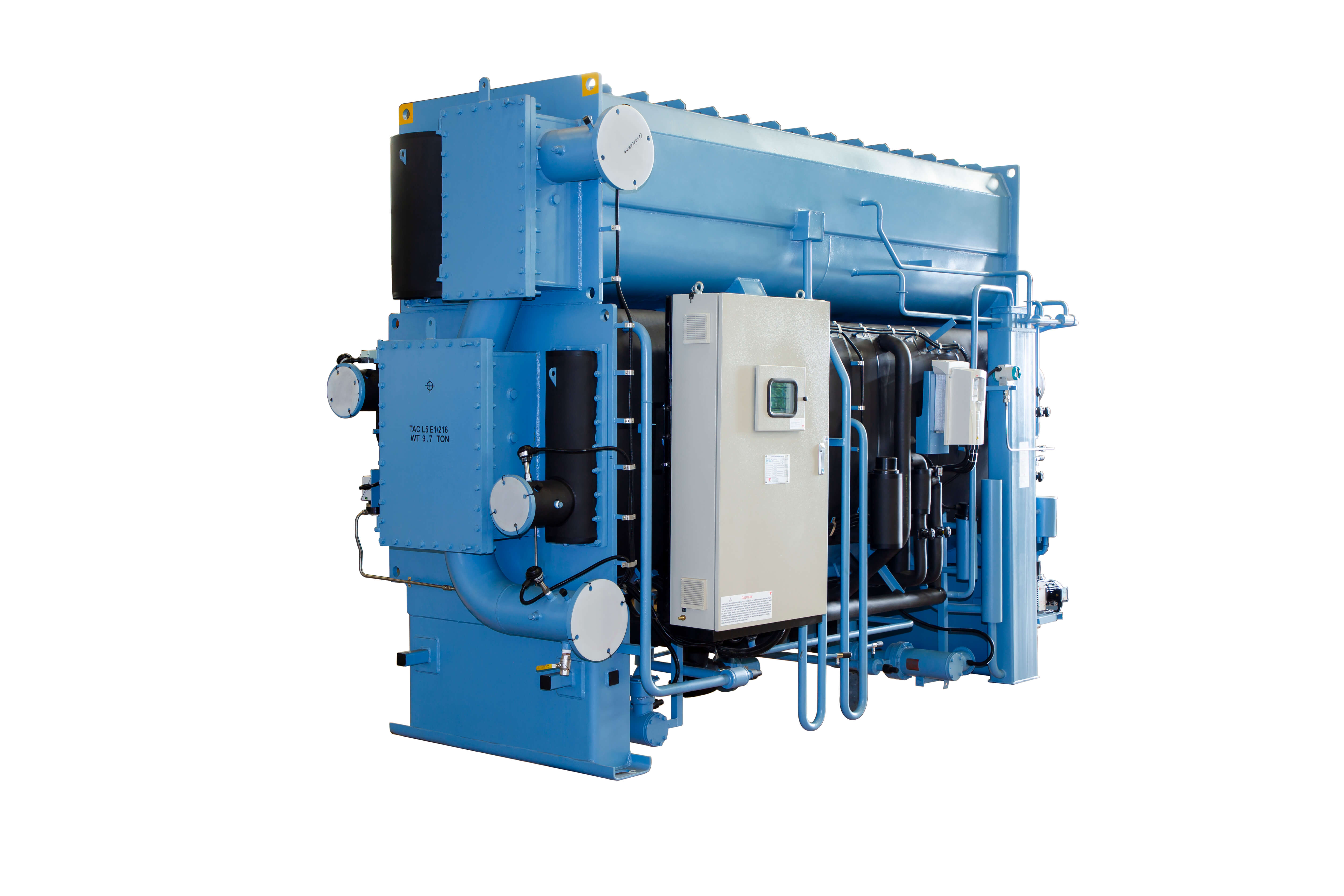
SINGLE EFFECT LOW TEMPERATURE HOT WATER DRIVEN VAPOUR ABSORPTION CHILLER
Heat Source: Hot Water
Inlet water temperature: 80OC – 120OC
COP: 0.8
Capacity: 180 – 1650 TR
Heat energy available in the form of
- Engine jacket water
- Hot water from solar collectors
- Process condensate
- Flue gas recovery from incinerators
- Process heat recovery
- Fuel cells
REFERENCES
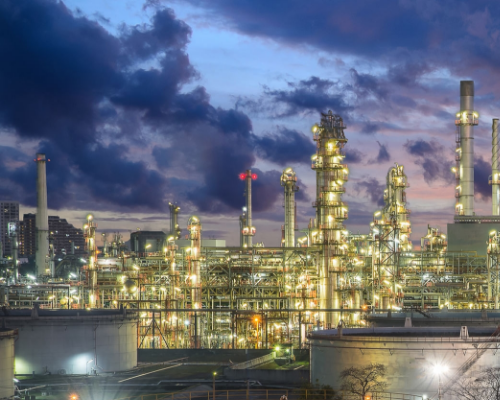
Manali Petrochemical Ltd
Location: India
Chiller Type: Low temperature hot water driven vapour absorption chiller
Capacity: 152 TR
No.of machine: 1
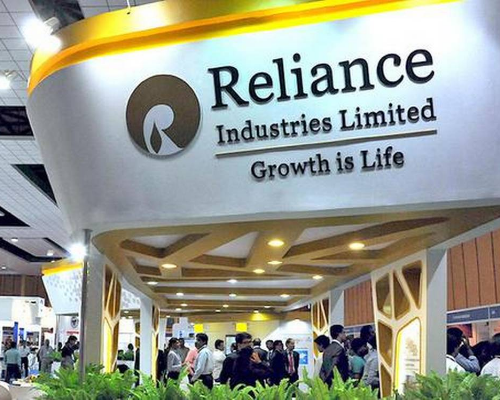
Reliance Industries Ltd
Location: India
Chiller Type: Single effect steam driven vapour absorption chiller
Capacity: 100 TR
No.of machine: 1
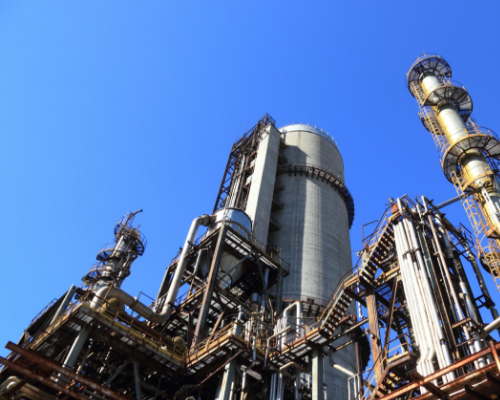
Indorama Pterochem Ltd
Location: Thailand
Chiller Type: Single effect steam driven vapour absorption chiller
Capacity: 270 TR
No.of machine: 1
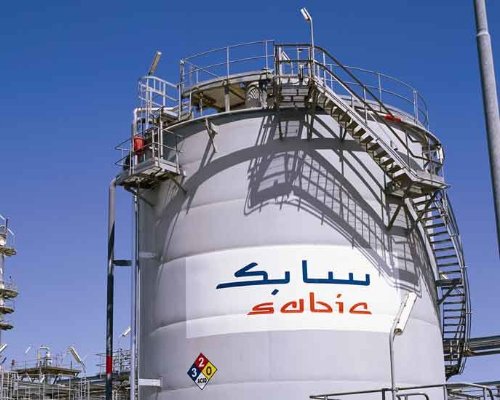
Yanpet
Location: Saudi Arabia
Chiller Type: Single effect steam driven vapour absorption chiller
Capacity: 1961 TR
No.of machine: 1