Modern processing equipment in the dairy industry accounts for about 40% of its total energy consumption. Thermax’s absorption and process cooling machines, when employed for chilling, pasteurisation, and storage can offer huge operational and energy savings.
DAIRY PROCESSING
Thermax’s cooling solutions deployed across processes help the dairy industry meet its demands at optimised energy costs
DAIRY PROCESSING
BULK MILK COOLING
Replacing conventional bulk milk cooler with Thermax’s absorption chiller-heater solution cools the milk instantly from 35°C to 3.5°C as against conventional bulk milk cooler which takes 4.5 hours. The instant cooling substantially improves the quality of raw milk by minimising bacterial growth. The same machine (Absorption Chiller-Heater) can be used to generate hot water for cleaning in place (CIP), hence eliminating the need for a separate hot water generation system. Replacing conventional condenser in the bulk milk cooling circuit with Thermax’s evaporative condenser can offer uninterrupted productivity and water savings.
SMART COLD ROOMS
Replacing conventional ammonia chiller in cold room with Thermax’s hybrid absorption chiller results in substantial power savings of almost 50% with a comparatively smaller footprint.Cooling milk accounts for most of the energy consumption in the dairy industry. The industry heavily relies on refrigeration and storage systems to maintain the quality of the milk and eliminate bacterial growth.
RAW MILK CHILLING PLANT
Thermax’s vapour absorption chiller helps to reduce refrigeration load on ammonia chiller by cooling water from 8°C to 3.5°C. This results in considerable operational savings and energy optimisation.
REPLACING IBT IN RAW MILK PLANT WITH ABSORPTION CHILLER
Replacing conventional IBT (Ice Bank Tank) and ammonia chiller system with Thermax’s 1°C chilled water vapour absorption chiller gives substantial operational savings. The initial cost also comes down as there is a remarkable reduction in the capacity of (standby) diesel generator.
PASTEURISATION
Thermax’s vapour absorption chiller-heater generates chilled water at 1°C & hot water at 85°C simultaneously, which leads to substantial savings in heat input and reduction in cooling tower capacity. The chiller-heater eliminates the dependency on multiple equipment for cooling and heating requirements along with overall reduction in energy costs. Integrating Thermax’s condenser in the pasteuriser offers energy optimisation coupled with water savings.
- More than 80% savings in electricity consumption which reduces dependency on unreliable grid power & fossil fuel
- More than 25% savings in operational cost
- Uses water as refrigerant. Hence, no CFCs & HCFCs are involved
- Zero ozone depletion potential
- Zero global warming potential with reduction in carbon footprints
- Quiet Operation (< 85 db)
- Low maintenance cost
- Highly reliable & long life
- Wide range of operation from 95°C to -40°C
- 80% Depreciation benefit
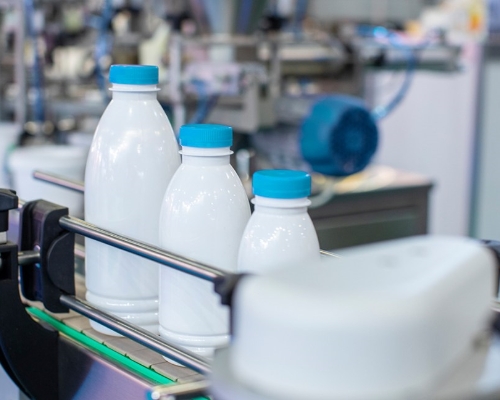
BENEFITS
- More than 80% savings in electricity consumption
- More than 25% savings in operational cost
- Low maintenance cost
- Wide range of operation from 95°C to -40°C
- Water savings
To know more about the application and benefits of our solutions, contact our experts now
OUR OFFERINGS
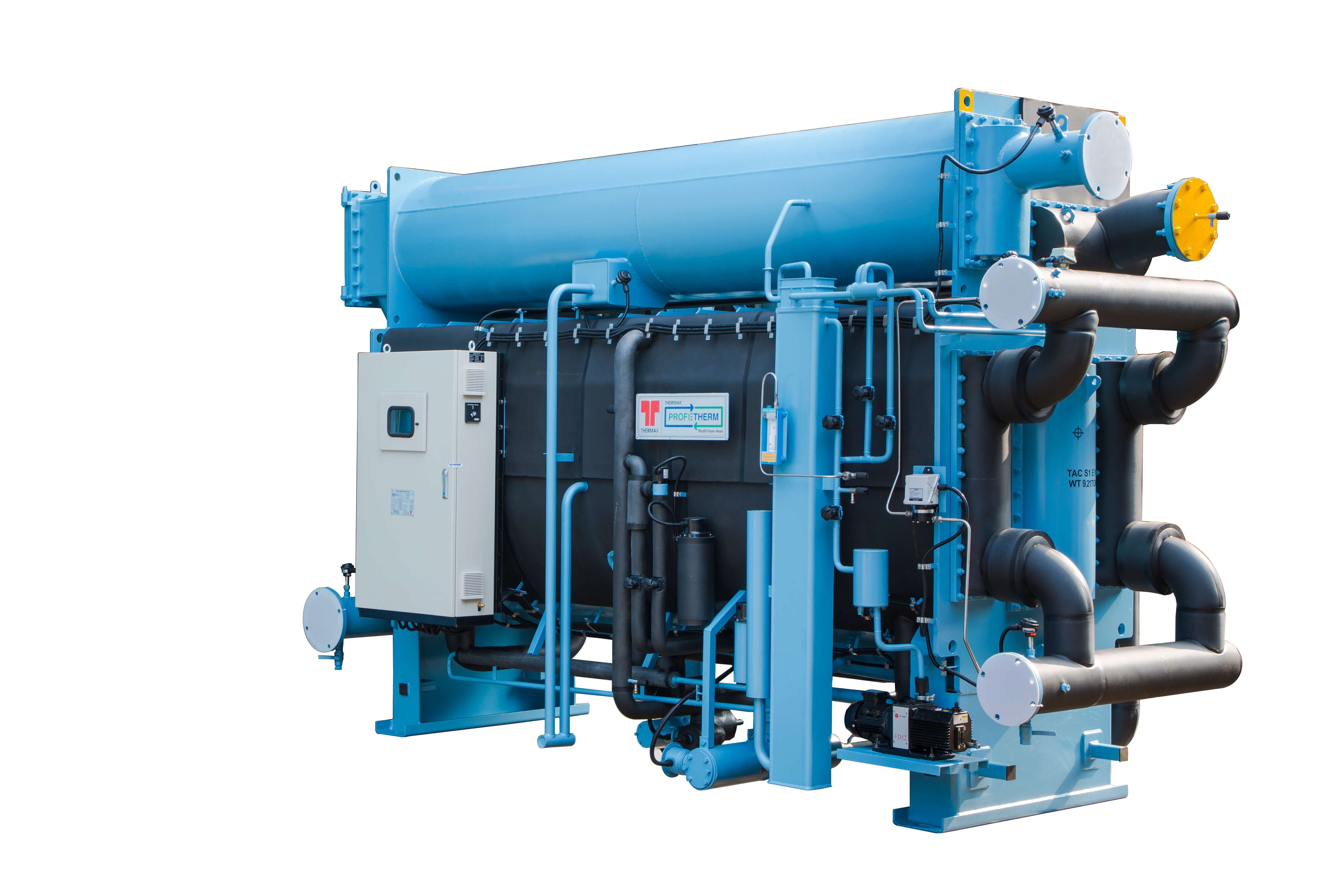
SINGLE EFFECT STEAM DRIVEN VAPOUR ABSORPTION CHILLER
Heat Source: Steam
Pressure: 0 bar.g – 3.5 bar.g
COP: 0.8
Capacity: 100 – 3500 TR
Heat energy available in the form of (LP- low pressure)
- LP vapour (0.1 bar.g, 103OC) coming from continuous polymerisation process in textile industry
- LP steam generated from potato fryer, instant noodle plant etc.
- LP Steam extraction from steam turbine in power plants
- Flash steam recovery
DOUBLE EFFECT STEAM FIRED VAPOUR ABSORPTION CHILLER
Heat Source: Steam
Pressure: 3 bar.g – 10.5 bar.g
COP: 1.5
Capacity: 50 – 3500 TR
Heat energy available in the form of
- Steam from boiler
- Steam from processes
- Steam from cogeneration plants
- Extraction from steam turbine
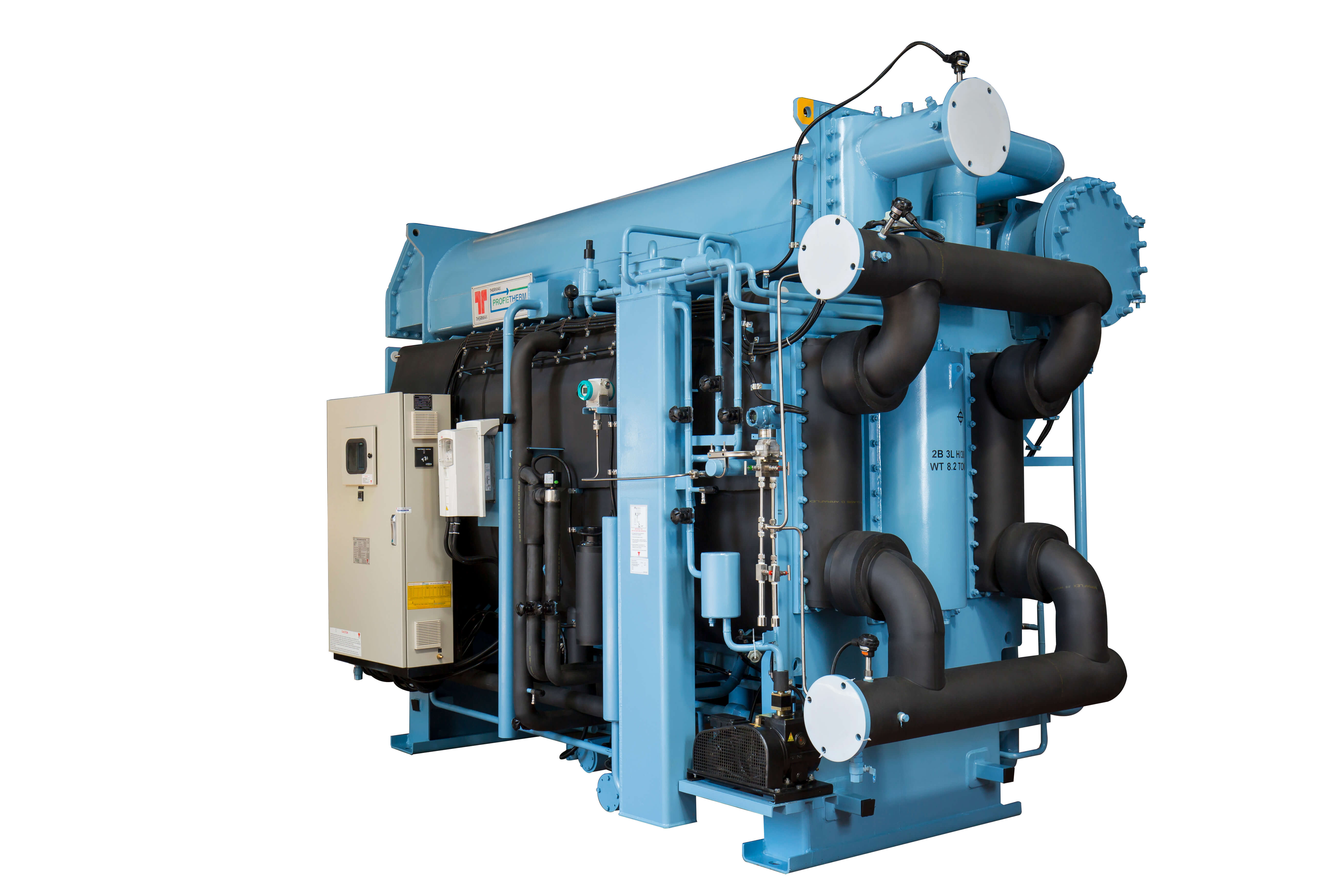
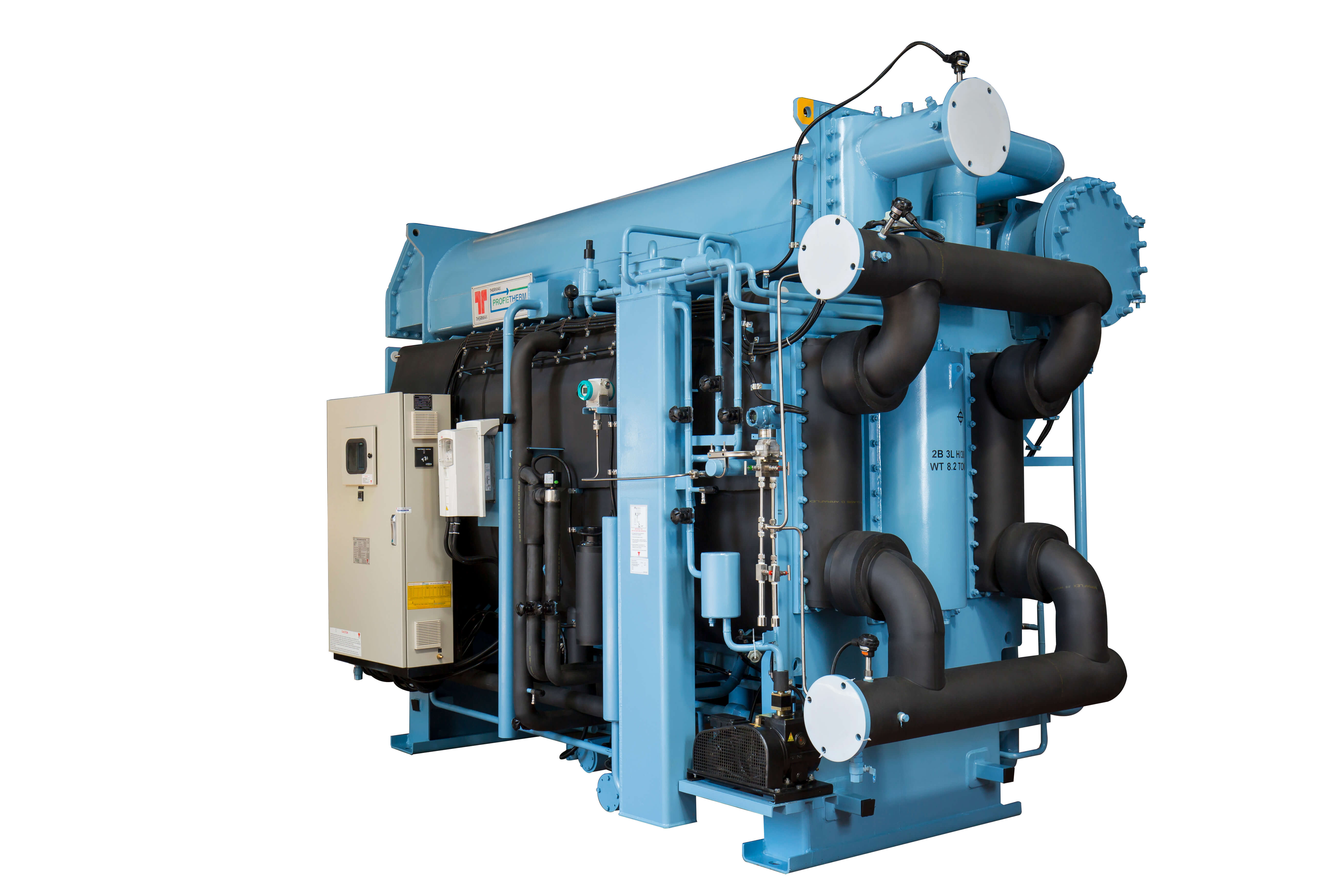
DOUBLE EFFECT STEAM FIRED VAPOUR ABSORPTION CHILLER
Heat Source: Steam
Pressure: 3 bar.g – 10.5 bar.g
COP: 1.5
Capacity: 50 – 3500 TR
Heat energy available in the form of
- Steam from boiler
- Steam from processes
- Steam from cogeneration plants
- Extraction from steam turbine
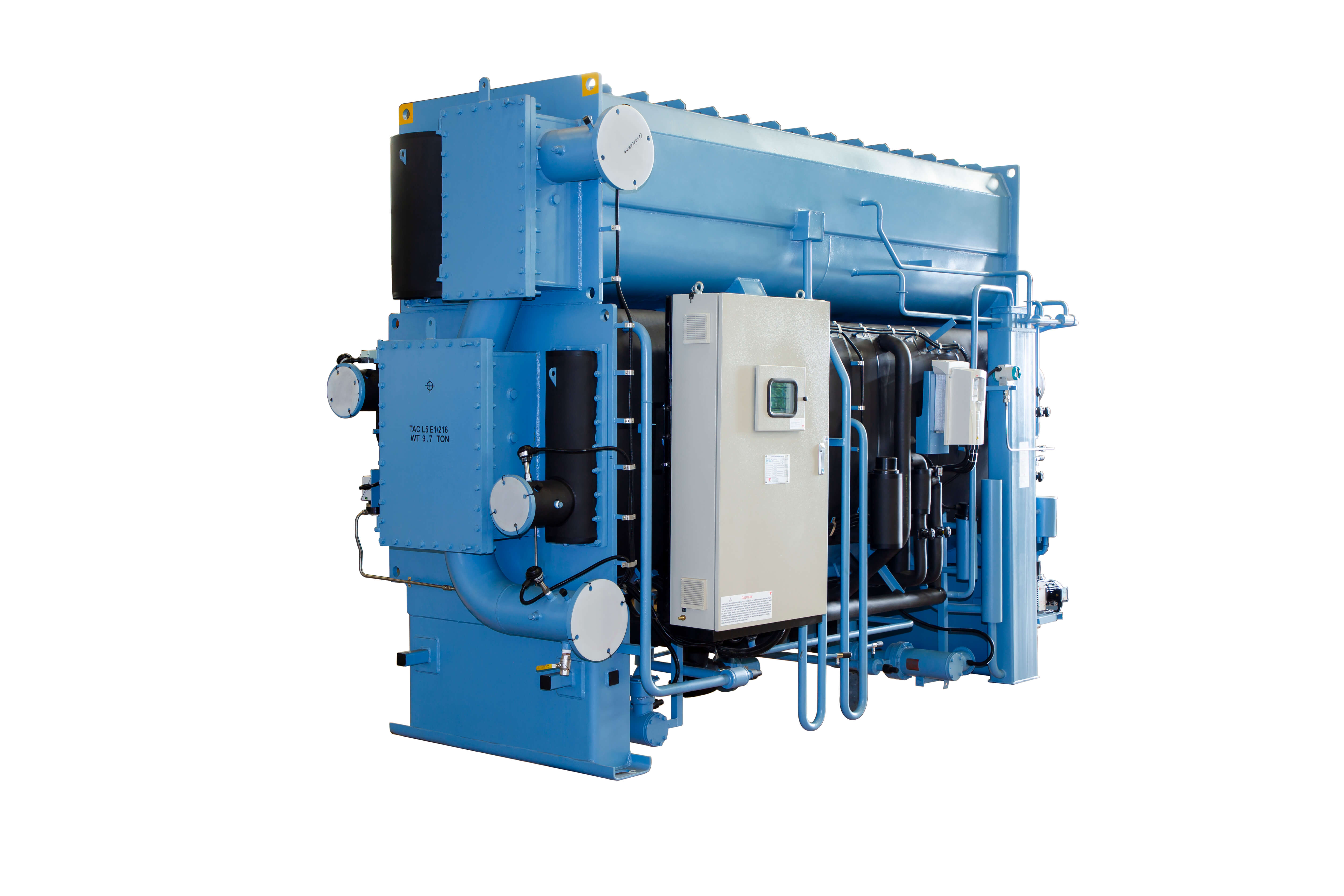
SINGLE EFFECT LOW TEMPERATURE HOT WATER DRIVEN VAPOUR ABSORPTION CHILLER
Heat Source: Hot Water
Inlet water temperature: 80OC – 120OC
COP: 0.8
Capacity: 180 – 1650 TR
Heat energy available in the form of
- Engine jacket water
- Hot water from solar collectors
- Process condensate
- Flue gas recovery from incinerators
- Process heat recovery
- Fuel cells
DOUBLE EFFECT DIRECT FIRED ABSORPTION CHILLER
Heat Source: Direct Fuel Firing
COP: 1.5
Capacity: 50 – 3000 TR
Heat energy available in the form of
- Natural gas
- LPG
- Propane
- Town gas
- Kerosene
- High speed diesel
- Oil
- Biogas
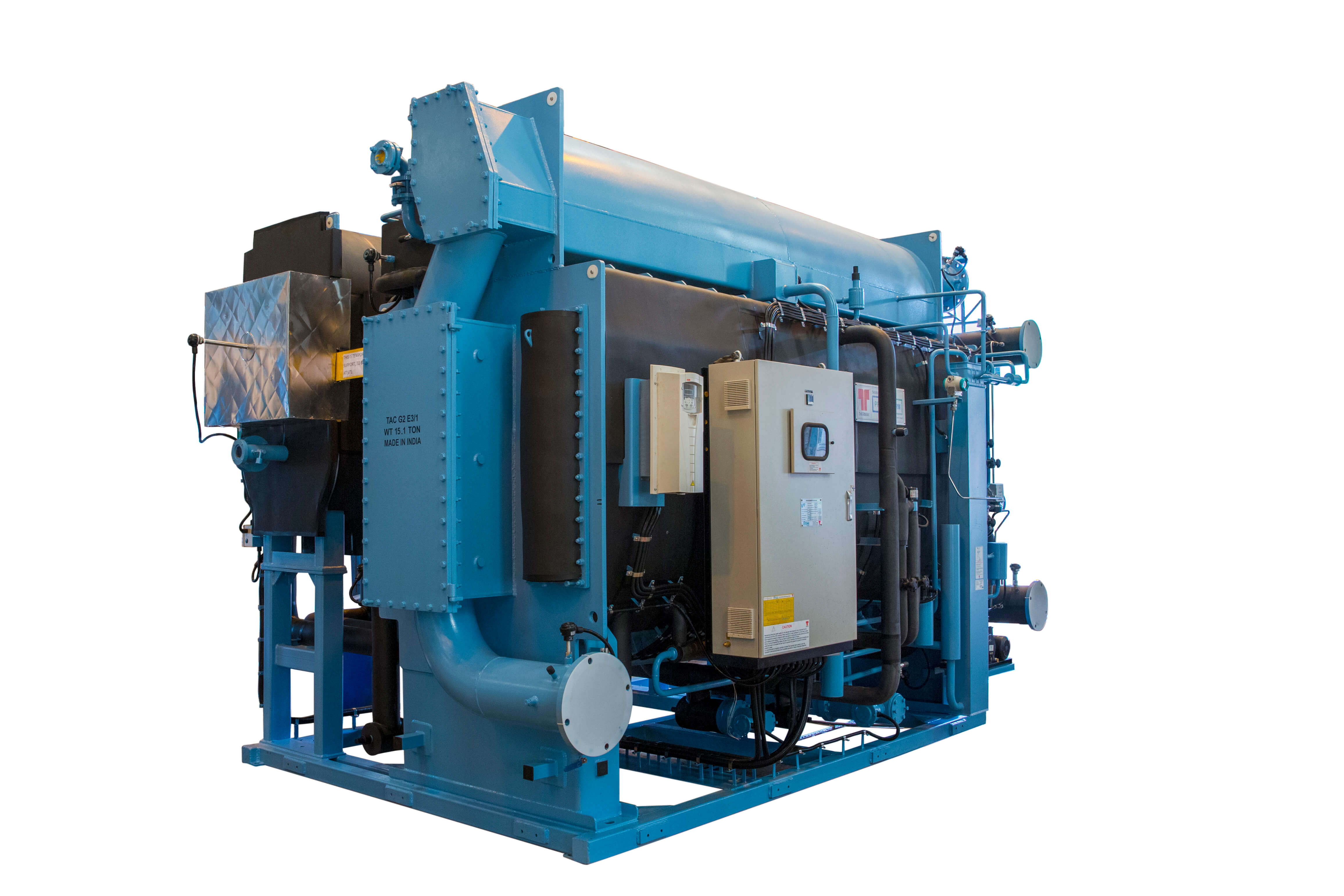
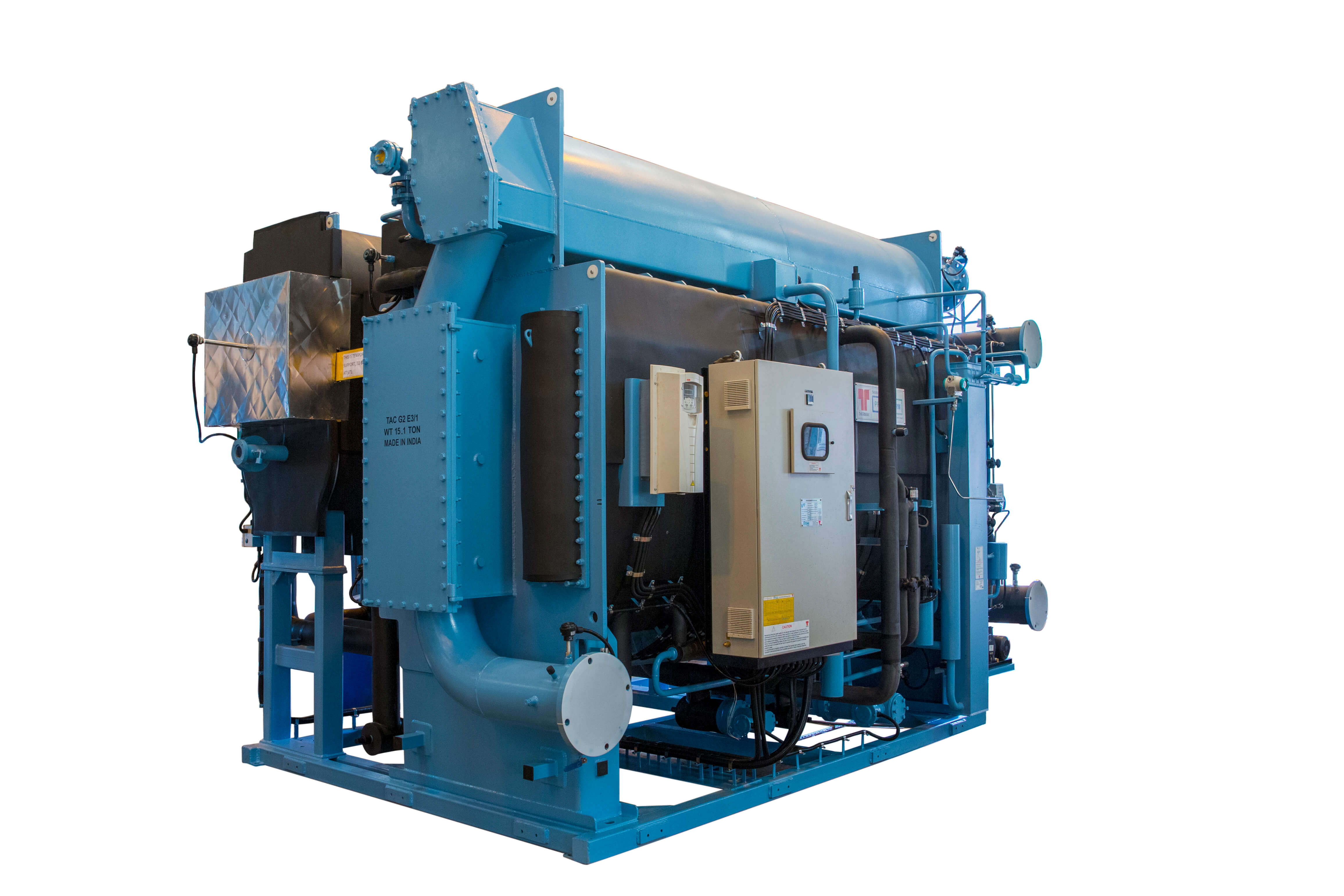
DOUBLE EFFECT DIRECT FIRED ABSORPTION CHILLER
Heat Source: Direct Fuel Firing
COP: 1.5
Capacity: 50 – 3000 TR
Heat energy available in the form of
- Natural gas
- LPG
- Propane
- Town gas
- Kerosene
- High speed diesel
- Oil
- Biogas
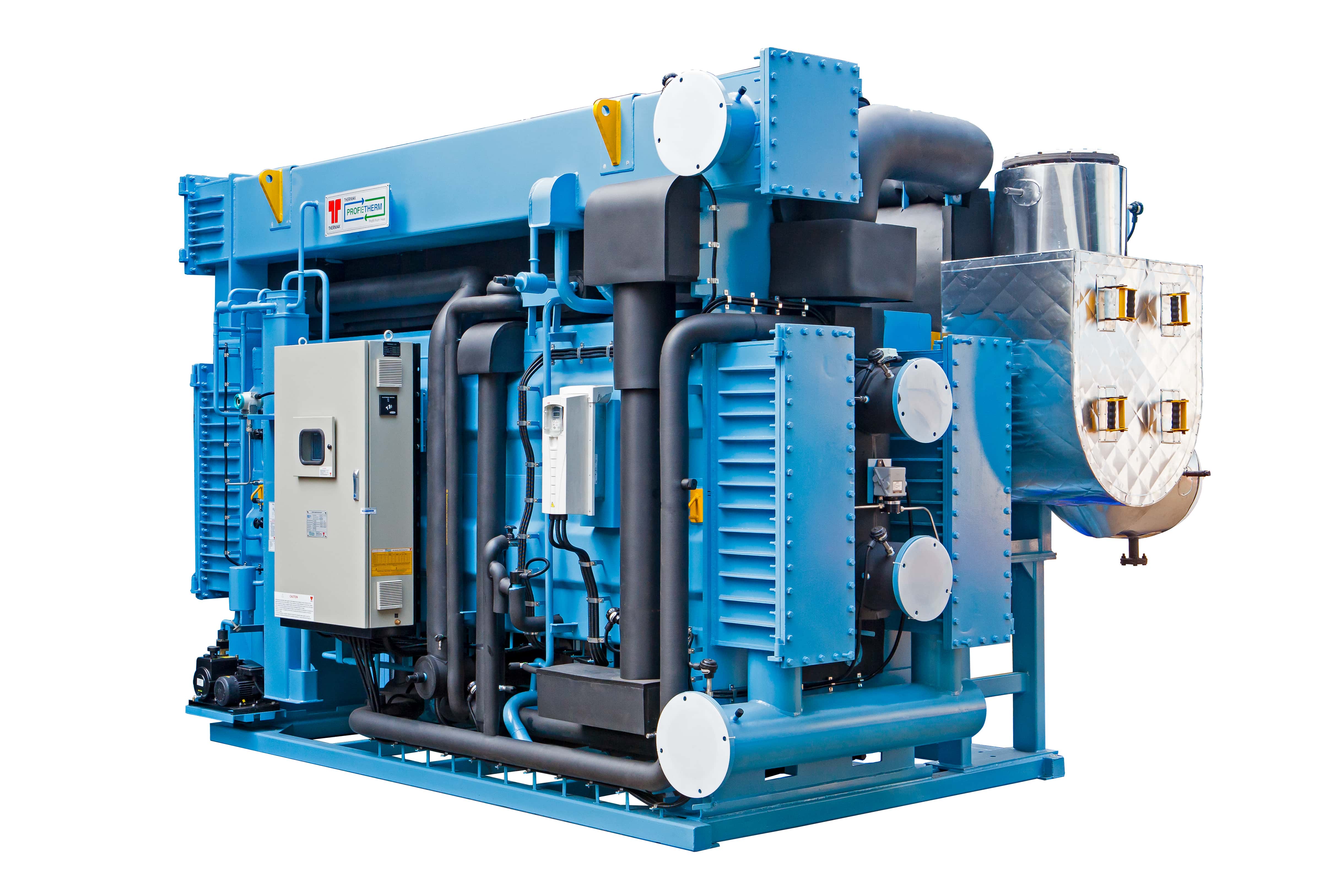
DOUBLE EFFECT EXHAUST FIRED ABSORPTION CHILLER
Heat Source: Exhaust Gas
Inlet Temperature: 250OC – 600OC
COP: 1.5
Capacity: 50 – 3500 TR
Heat energy available in the form of
- Flue gas from gas engines or diesel engines
- Flue gas from gas turbines
- Flue gas from micro turbines
- Flue gas from fuel cells
- Clean flue gas from ovens, furnaces, thermic fluid heaters etc.
HIGH EFFICIENCY CHILLER – HEATER
Heat Source: Steam, Hot Water, Direct Fuel Firing & Exhaust Gas
Capacity:
Cooling : 100 – 3500 TR
Heating : 100 Kw – 9 MW
Heat energy available in the form of
- Dry saturated steam – 3.0 – 10.0 Bar.g
- High temperature hot water -145 – 180OC
- Direct fuel firing – Gas / Oil / LPG / Propane)
- Exhaust gas (275 – 600OC)
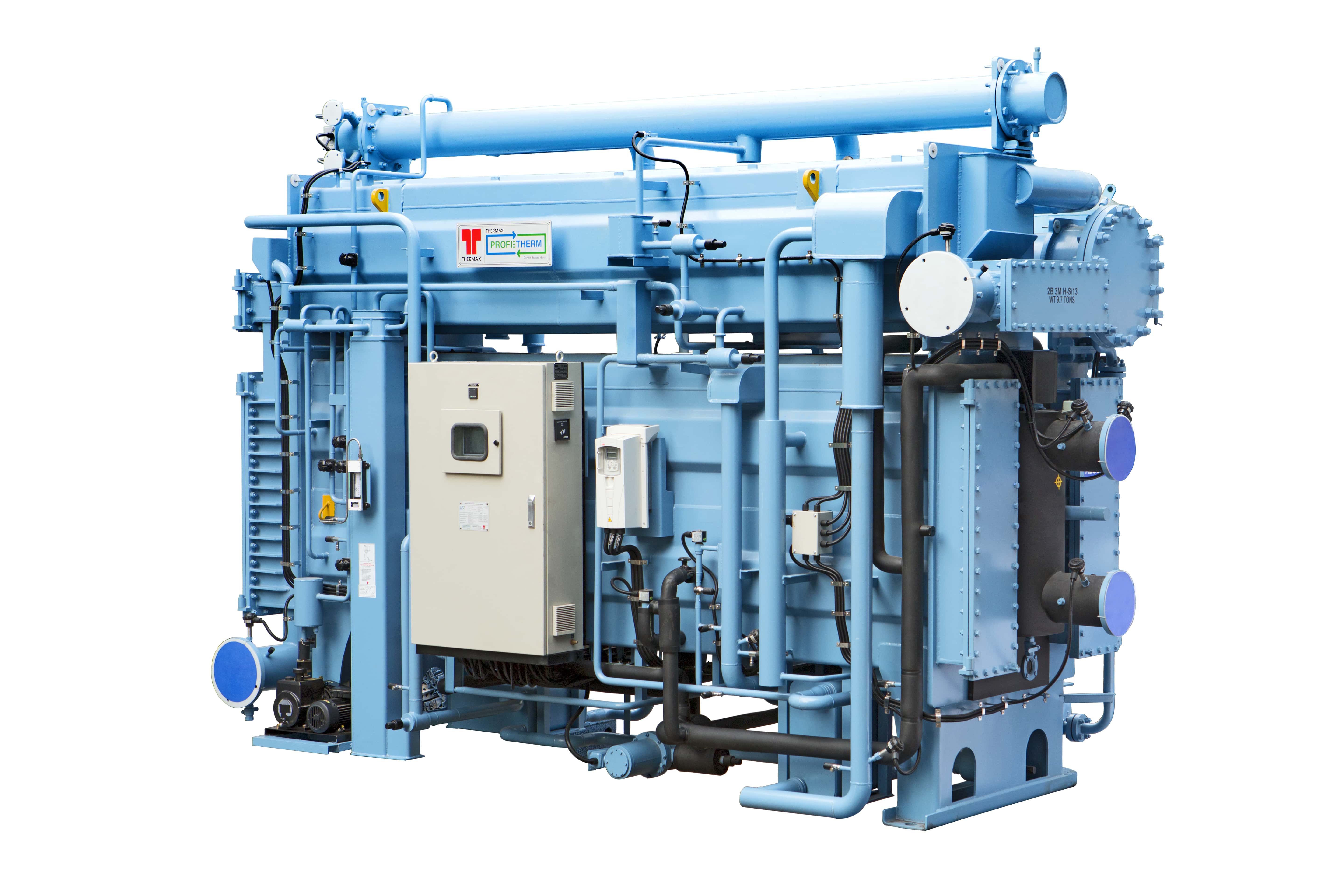
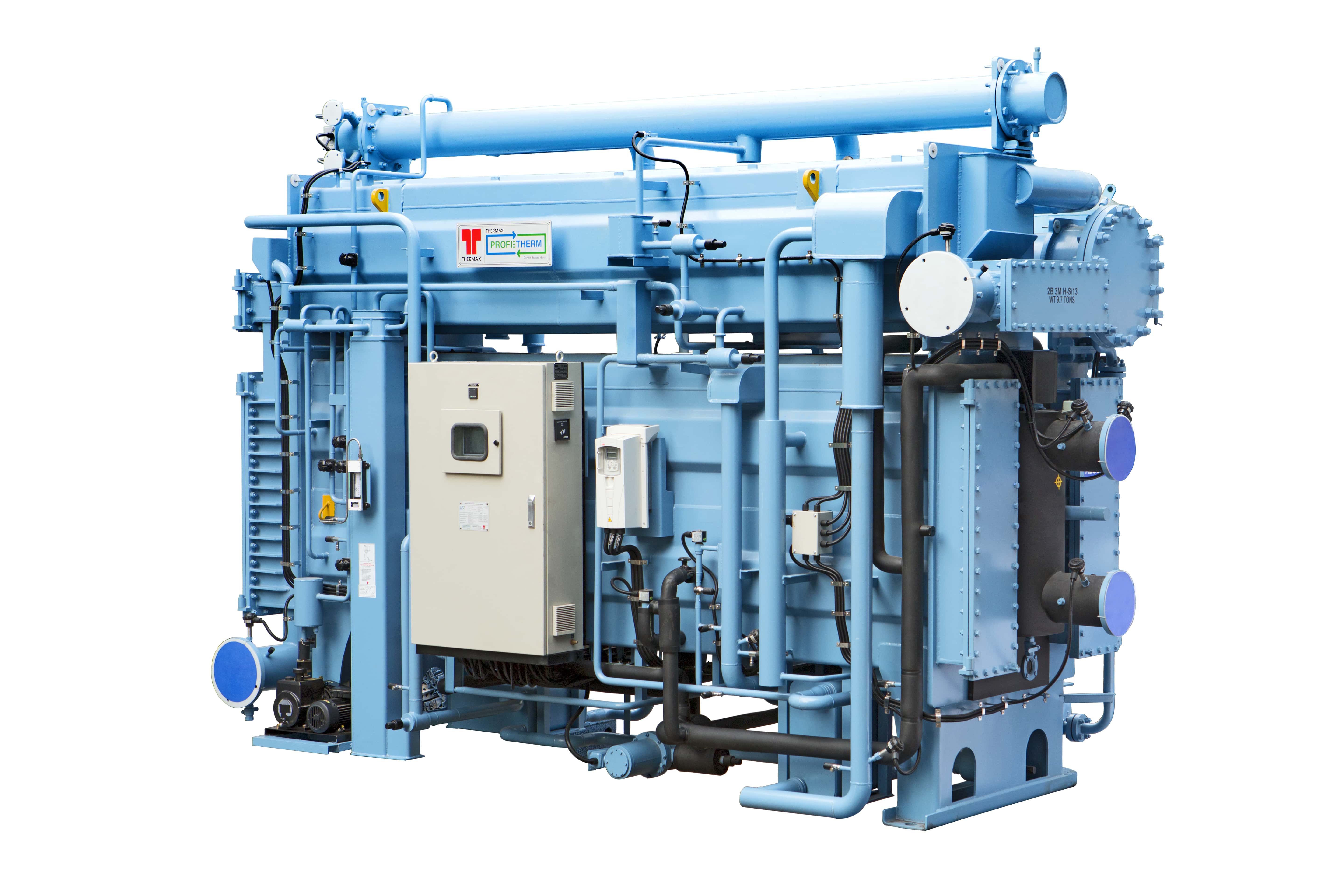
HIGH EFFICIENCY CHILLER – HEATER
Heat Source: Steam, Hot Water, Direct Fuel Firing & Exhaust Gas
Capacity:
Cooling : 100 – 3500 TR
Heating : 100 Kw – 9 MW
Heat energy available in the form of
- Dry saturated steam – 3.0 – 10.0 Bar.g
- High temperature hot water -145 – 180OC
- Direct fuel firing – Gas / Oil / LPG / Propane)
- Exhaust gas (275 – 600OC)
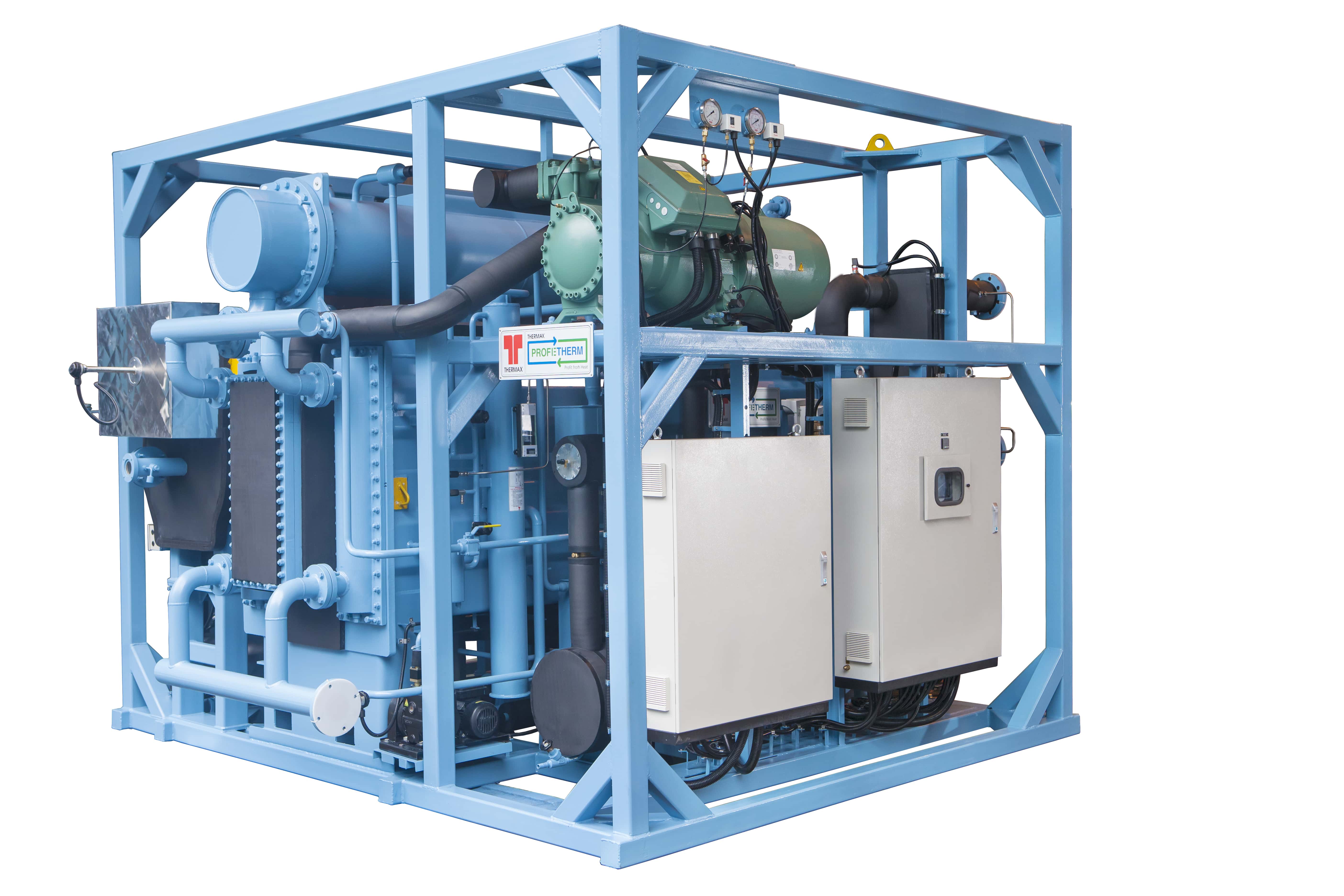
HYBRID CHILLER
Heat Source: Steam, Hot Water & Exhaust Gas
Capacity: 50 – 250 TR
BRINE TEMPERATURE: -5 to -25OC
Heat energy available in the form of
- Dry saturated steam (0.5 – 3.5 bar.g)
- Dry saturated steam (5.0 – 10.5 bar.g)
- Low temperature hot water (90 – 150OC)
- High temperature hot water (150 – 180OC)
- Exhaust gases (300 – 600OC)
ONE DEGREE VAPOUR ABSORPTION CHILLER
- Pure water at 1°C is delivered
- Simpler to erect, operate and maintain
- Special tubes used in evaporator to prevent freezing of water
- Sophisticated controls to ensure availability of chilled water flow and velocity
- 40% operational savings
- Generates chilled water at 1°C and hot water of up to 90°C simultaneously
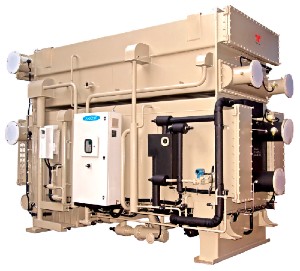
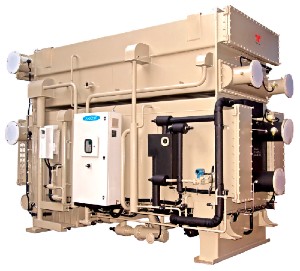
HYBRID CHILLER
- Pure water at 1°C is delivered
- Simpler to erect, operate and maintain
- Special tubes used in evaporator to prevent freezing of water
- Sophisticated controls to ensure availability of chilled water flow and velocity
- 40% operational savings
- Generates chilled water at 1°C and hot water of up to 90°C simultaneously
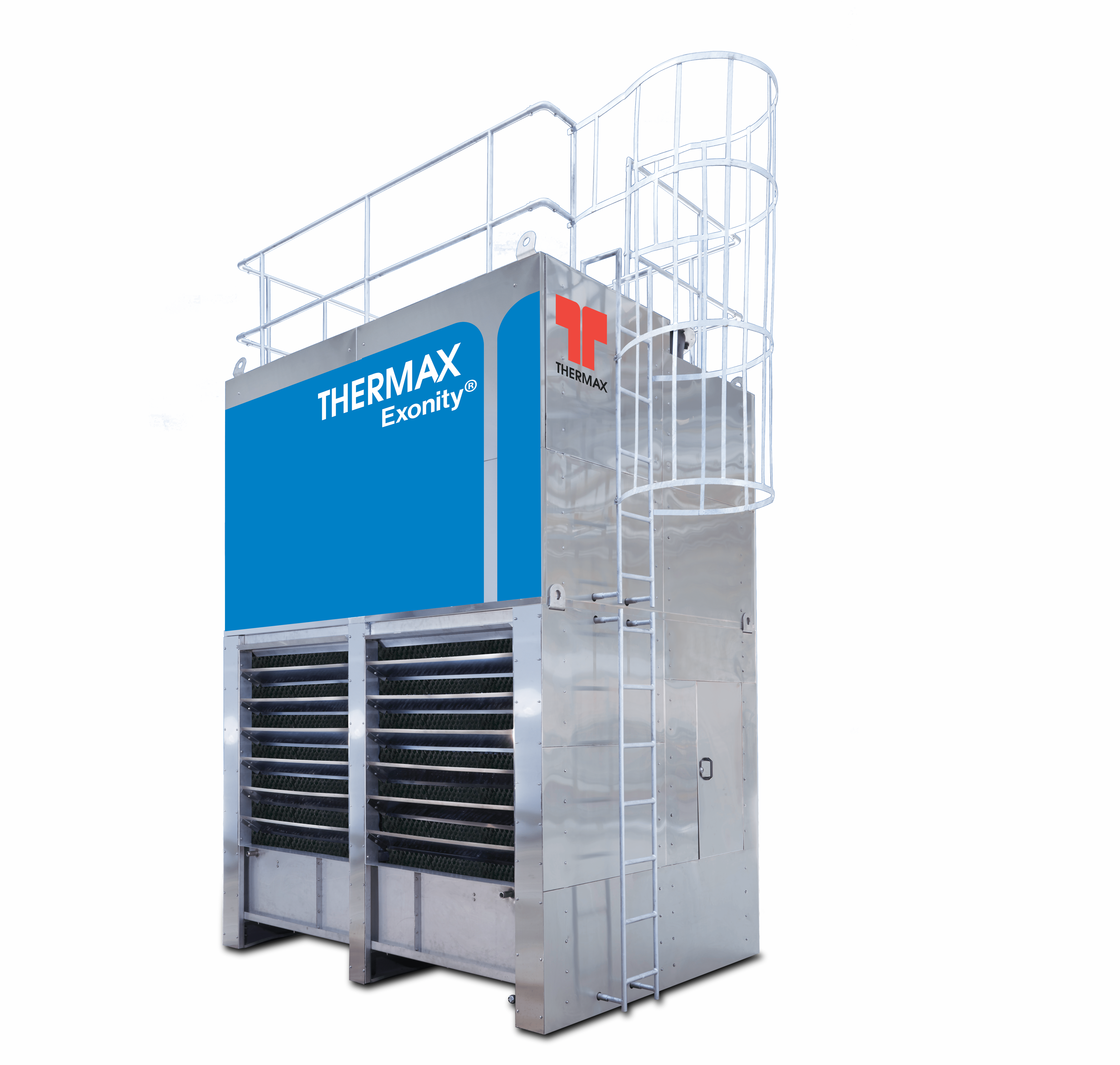
EVAPORATIVE CONDENSER
Product Features
- Replacement product against conventional systems (atmospheric condenser, shell & tube heat exchanger + cooling tower, plate heat exchanger + cooling tower)
- For ammonia/freon condensation at lower temperature
- Ideal for various refrigeration systems and climatic conditions
- Compatible with all types of refrigeration compressors i.e. reciprocating, screw, scroll, rotary and centrifugal
- Combined and counter flow technology available
- Modular construction allows plug & play installation for new and replacement units
Product Capacity: 50 TR and above
REFERENCES
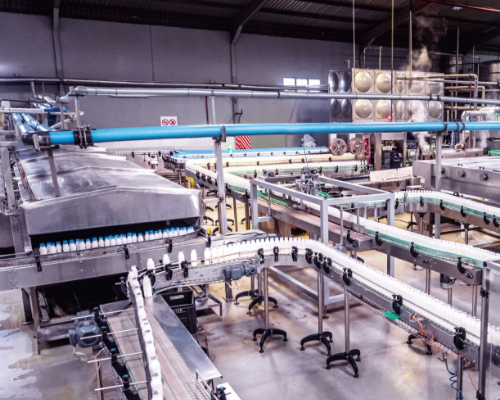
Hatsun Agro Product Ltd
Dairy
Location: India
Type: Double effect steam fired absorption Chiller
Capacity: 300 TR
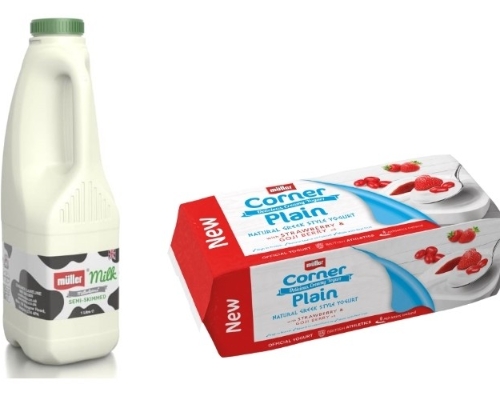
Mueller Foods
Dairy
Location: United Kingdom
Type: Low temperature hot water driven chiller
Capacity: 113.75 TR
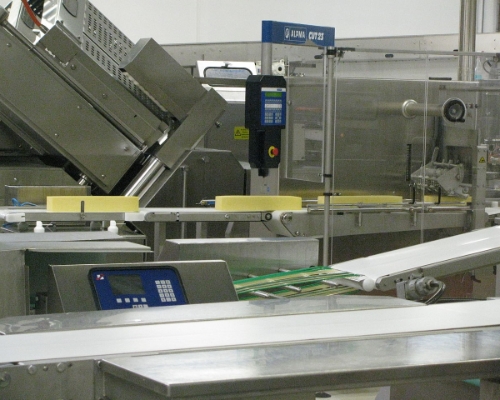
Heinrichstahler Milchwerke
Dairy
Location: Germany
Type : Double-effect steam fired absorption chillers
Capacity :600 TR
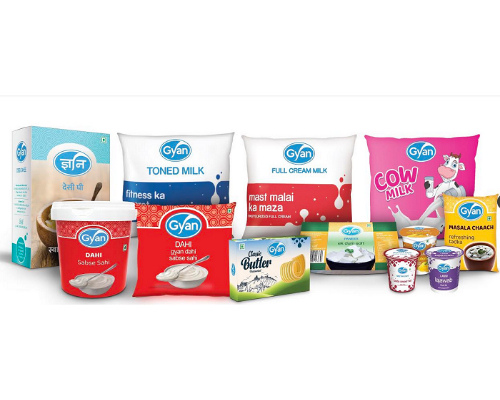
CP Milk
Dairy
Location: India
Type: Evaporative Condenser
Capacity: 500 KW
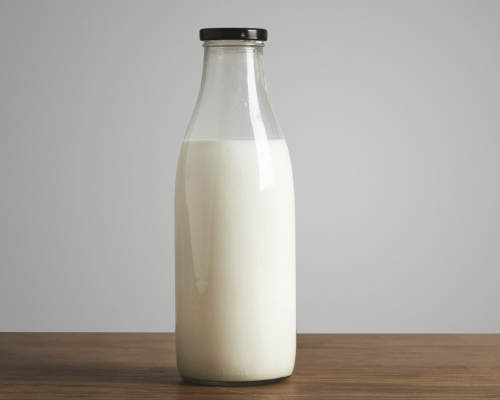
Narmada Dairy
Dairy
Location: India
Type: Evaporative Condenser
Capacity: 170 TR