CHEMICALS & FERTILISERS
Optimise energy use in chemicals & fertilisers plants with Thermax cooling and heating solutions, catering to your plant's processes sustainably
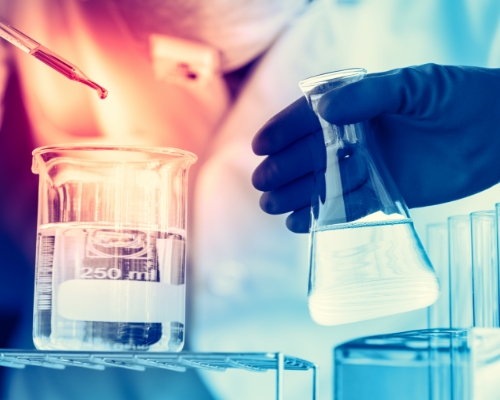
TRANSFORMING ENERGY UTILISATION OF CHEMICALS AND FERTILISERS INDUSTRY
- Paint industry
- - Solvent based paint production
- - Water based paint production
- Pesticide industry
- Fertiliser industry
PAINT MANUFACTURING
- Solvent Based Paint Production
- Sand mill or dispersion unit cooling
- Temperature & humidity control / air conditioning of plant & packaging area
- Maintaining temperature of monomer tank
- Maintaining temperature of reactors / mixing tanks
- Water Based Paint Production
- Sand mill or dispersion unit cooling
- Temperature & humidity control / air conditioning of plant & packaging area
SOLVENT BASED PAINT PRODUCTION
- Sand mills and dispersion units need to be kept at lower temperature as due to friction heat is generated and may affect the quality of paint. Depending on the requirement chilled water or cooling tower water is used.
- These units are jacketed tanks, use of conventional cooling towers may increase the chances of scaling and fouling inside the jackets of tanks (heat exchanger). Hence, it is advisable for paint manufacturers to use closed loop cooling tower.
- The resins coming in the mixer generates heat due to chemical reaction and it is cooled by application of 10°C chilled water to maintain the inside temperature so that reaction occurs as desired.
- 7°C chilled water is supplied to the monomer tank to maintain low temperature of 20°C of the solution as it is highly inflammable
WATER BASED PAINT PRODUCTION
Sand mills and dispersion units need to be kept at lower temperature as due to friction heat is generated and may affect the quality of paint. Depending on the requirement chilled water or cooling tower water is used. These units are jacketed tanks, use of conventional cooling towers may increase the chances of scaling and fouling inside the jackets of tanks (heat exchanger). Hence, it is advisable for paint manufacturers to use closed loop cooling tower.PESTICIDE MANUFACTURING
- Reactor cooling
- Secondary condenser of distillation column
- Primary condenser of distillation column
- Solvent recovery
- Reboiler heating – Based on secondary recovery of cooling tower water / partial heating of reboiler
FERTILISER INDUSTRY
- Inlet air cooling
- Process air cooling
- SYN gas cooling
- CO2 cooling
COMFORT COOLING
Absorption cooling solutions find application in temperature and humidity control, air conditioning of plant and packaging area in the industry. Customised to deliver cooling at different temperatures, the solutions enhance reliability and efficiency of cooling in the plants.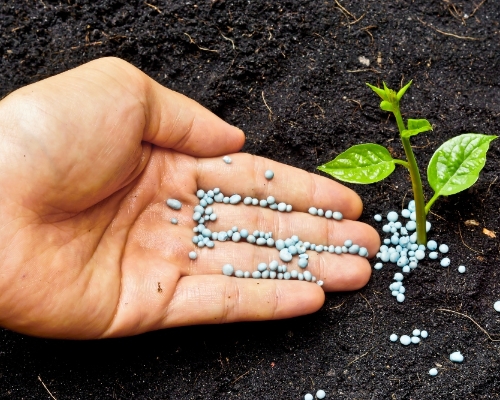
BENEFITS
- Increase in throughput & overall efficiency of the equipment
- Increased power generation & improvement in heat rate
- Increased compressor capacity
- Reduction of power or steam consumption
To know more about the application and benefits of our solutions, contact our experts now
OUR OFFERINGS
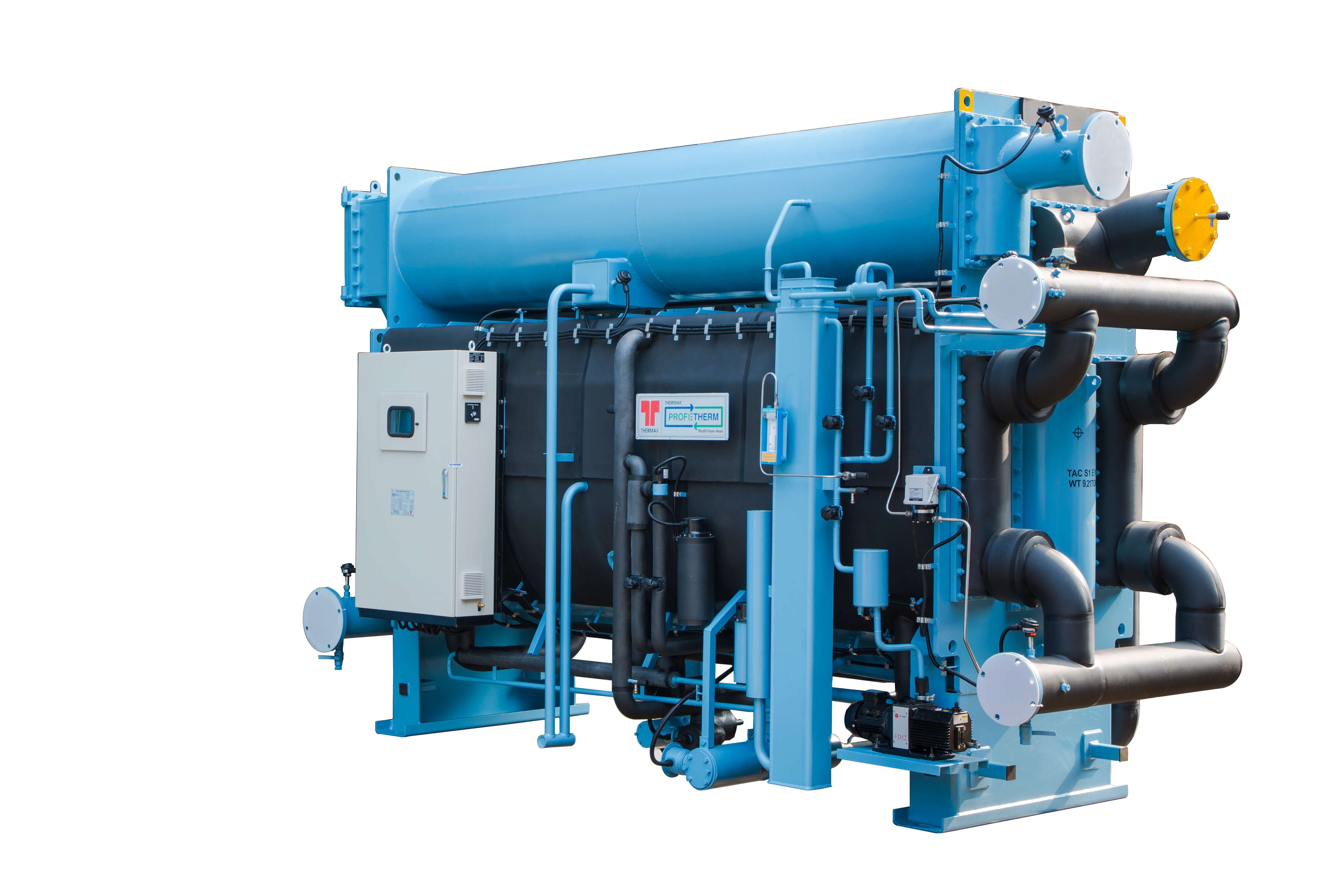
SINGLE EFFECT STEAM DRIVEN VAPOUR ABSORPTION CHILLER
Heat Source: Steam
Pressure: 0 bar.g – 3.5 bar.g
COP: 0.8
Capacity: 100 – 3500 TR
Heat energy available in the form of (LP- low pressure)
- LP vapour (0.1 bar.g, 103OC) coming from continuous polymerisation process in textile industry
- LP steam generated from potato fryer, instant noodle plant etc.
- LP Steam extraction from steam turbine in power plants
- Flash steam recovery
DOUBLE EFFECT STEAM FIRED VAPOUR ABSORPTION CHILLER
Heat Source: Steam
Pressure: 3 bar.g – 10.5 bar.g
COP: 1.5
Capacity: 50 – 3500 TR
Heat energy available in the form of
- Steam from boiler
- Steam from processes
- Steam from cogeneration plants
- Extraction from steam turbine
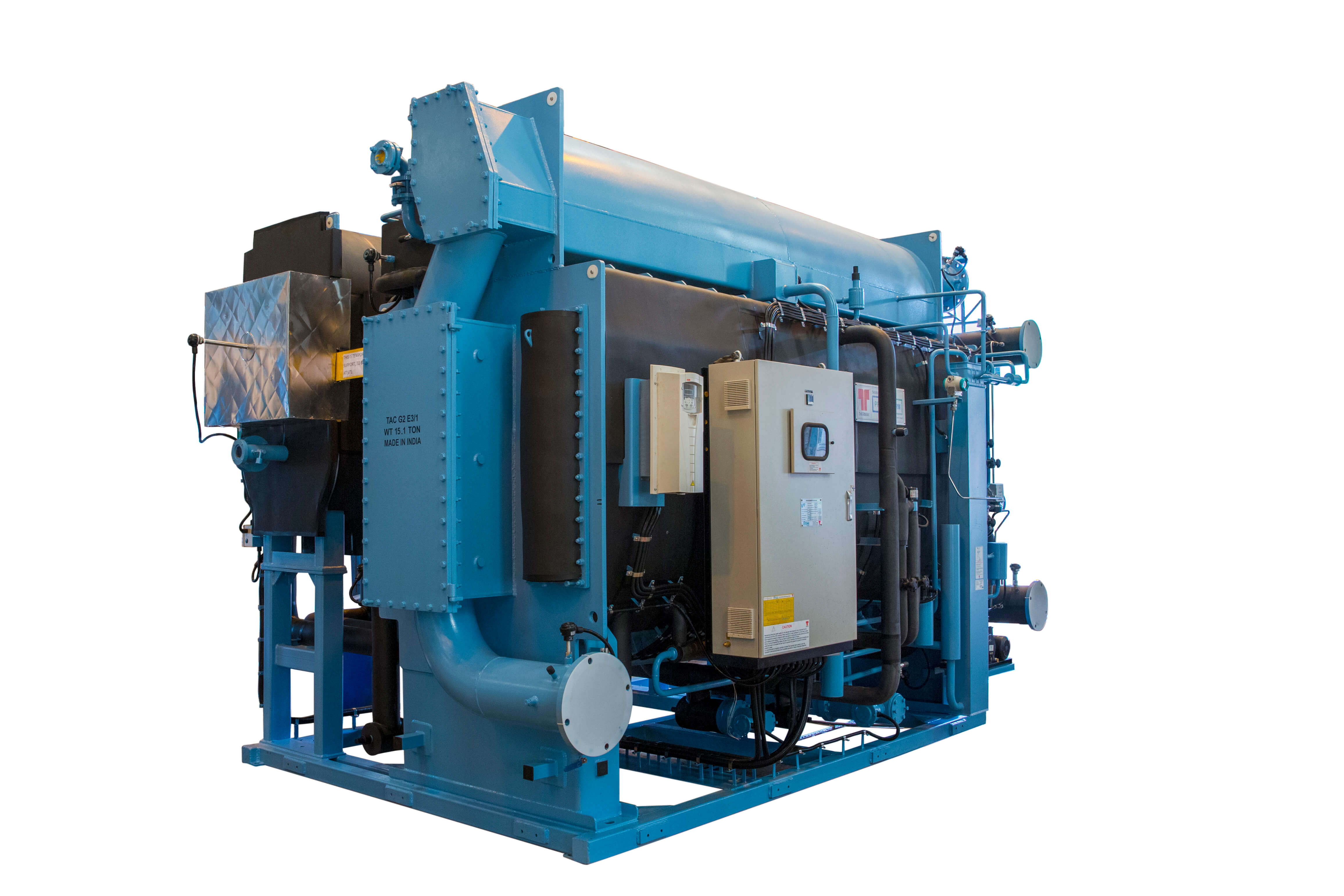
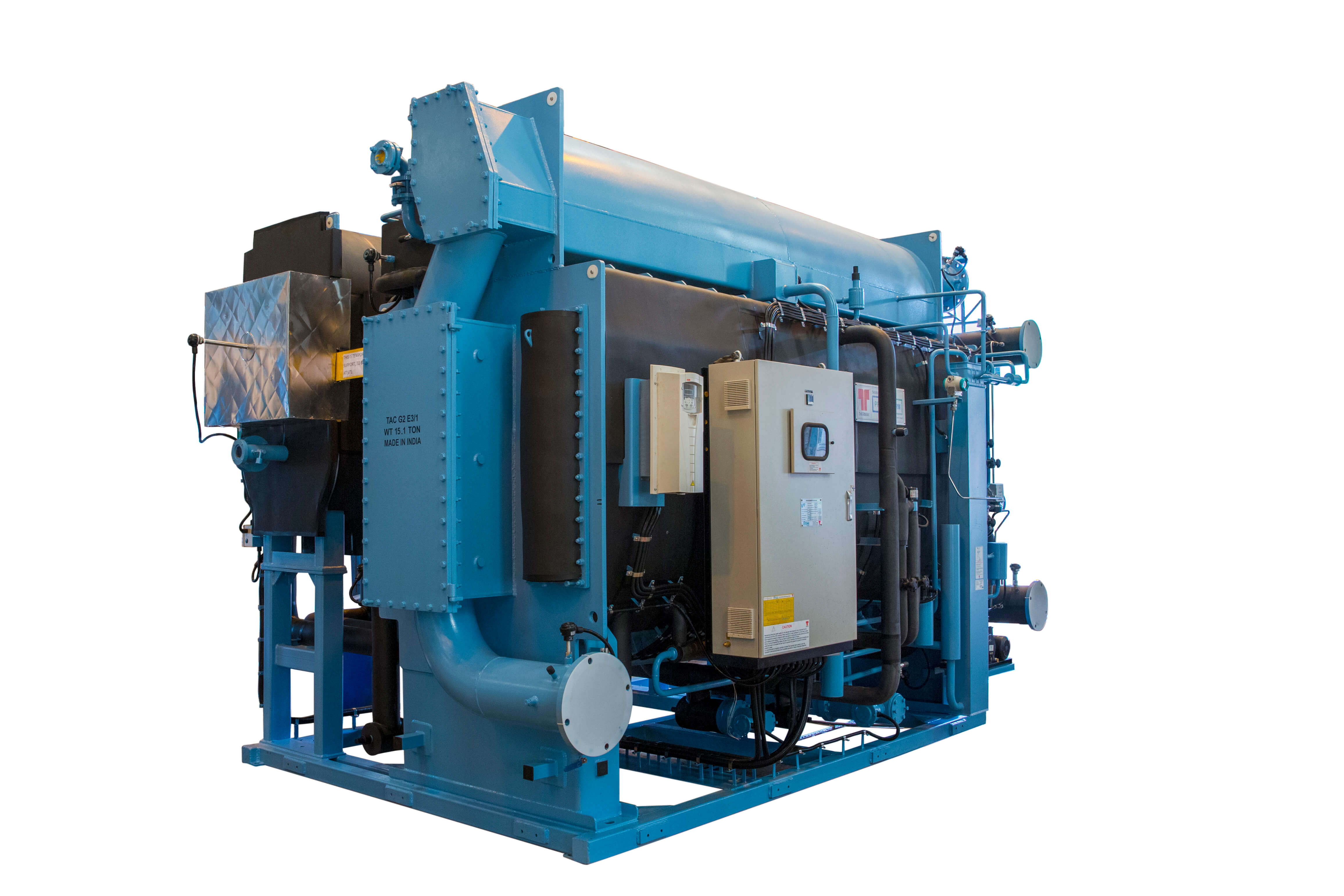
DOUBLE EFFECT STEAM FIRED VAPOUR ABSORPTION CHILLER
Heat Source: Steam
Pressure: 3 bar.g – 10.5 bar.g
COP: 1.5
Capacity: 50 – 3500 TR
Heat energy available in the form of
- Steam from boiler
- Steam from processes
- Steam from cogeneration plants
- Extraction from steam turbine
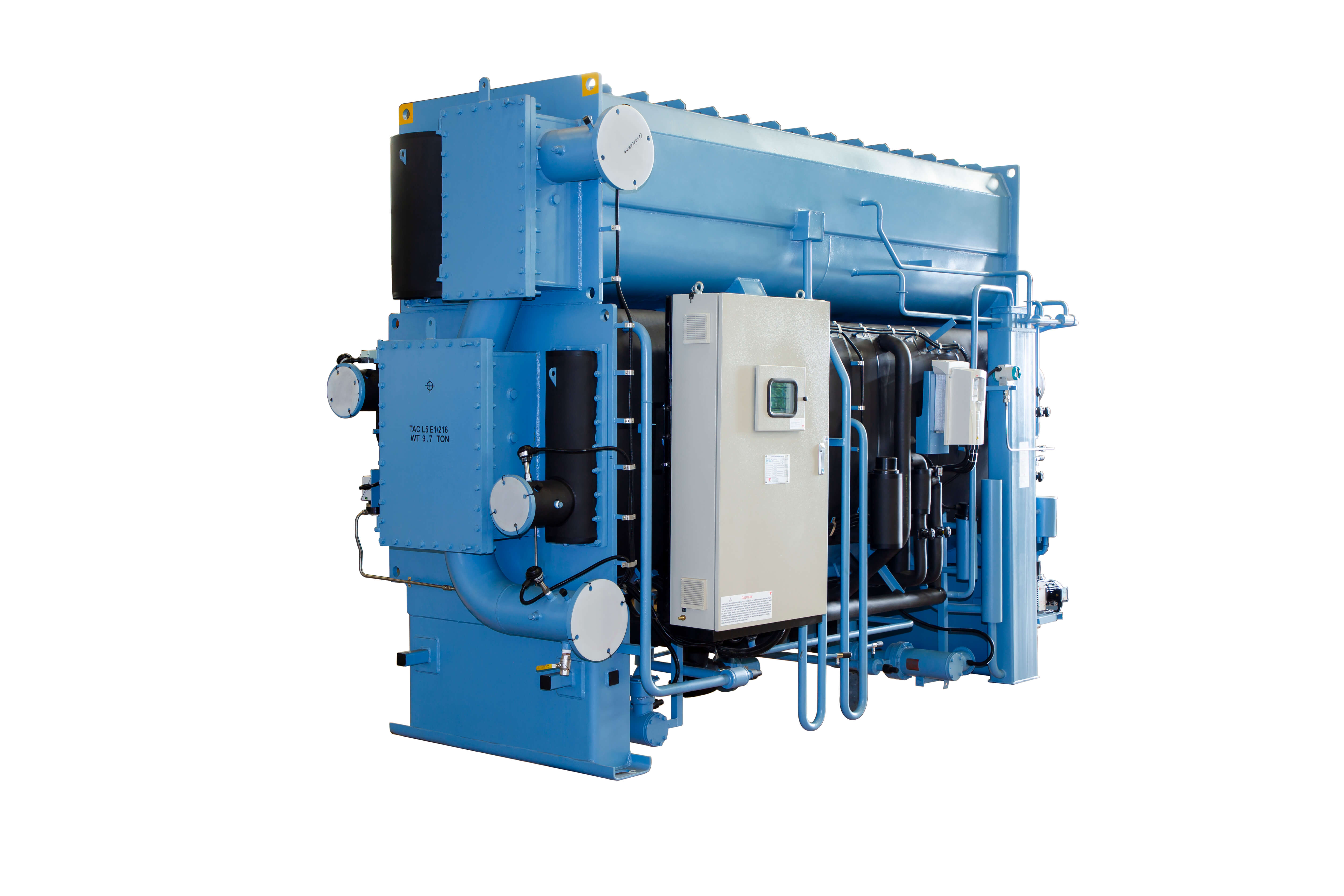
SINGLE EFFECT LOW TEMPERATURE HOT WATER DRIVEN VAPOUR ABSORPTION CHILLER
Heat Source: Hot Water
Inlet water temperature: 80OC – 120OC
COP: 0.8
Capacity: 180 – 1650 TR
Heat energy available in the form of
- Engine jacket water
- Hot water from solar collectors
- Process condensate
- Flue gas recovery from incinerators
- Process heat recovery
- Fuel cells
DOUBLE EFFECT DIRECT FIRED ABSORPTION CHILLER
Heat Source: Direct Fuel Firing
COP: 1.5
Capacity: 50 – 3000 TR
Heat energy available in the form of
- Natural gas
- LPG
- Propane
- Town gas
- Kerosene
- High speed diesel
- Oil
- Biogas
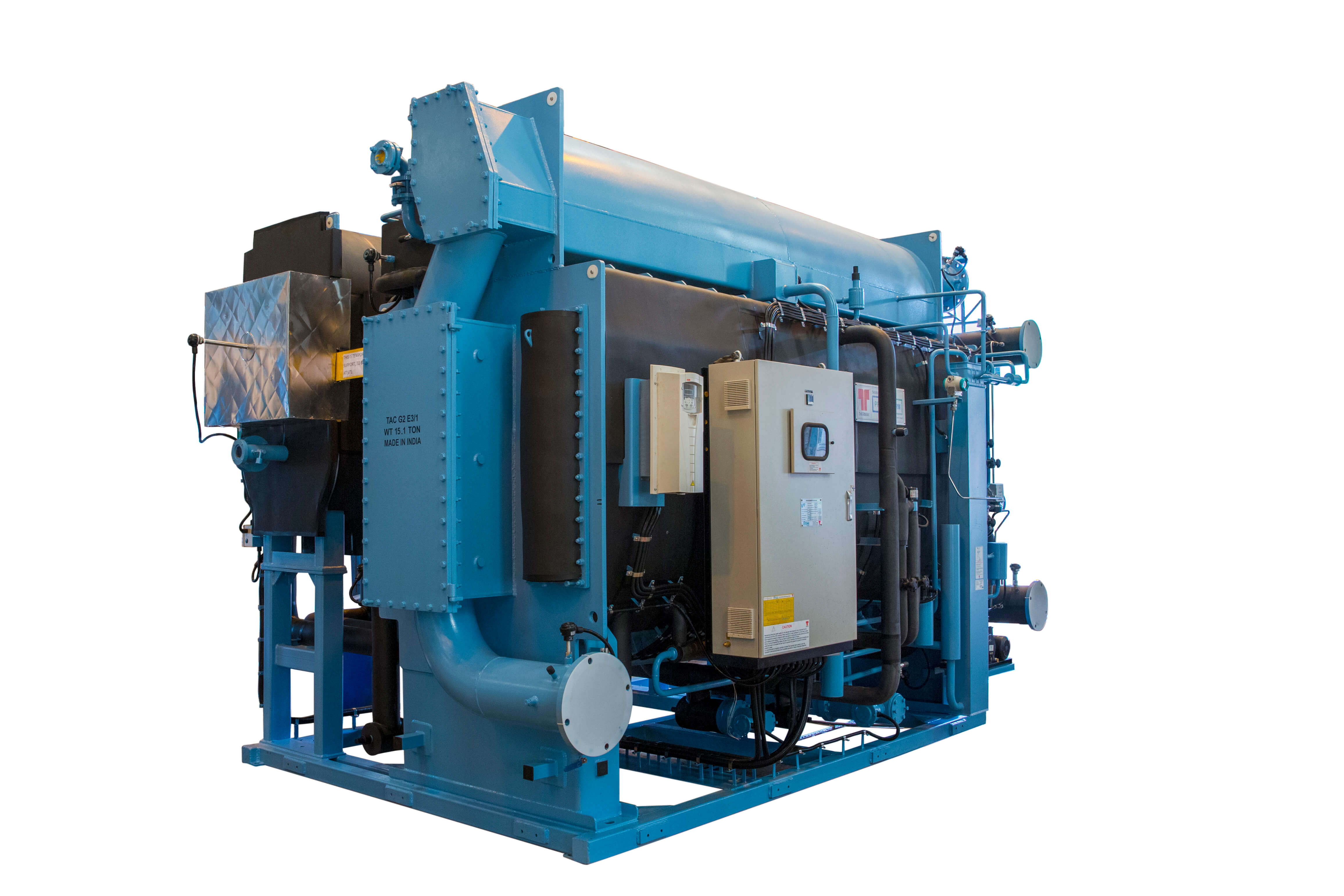
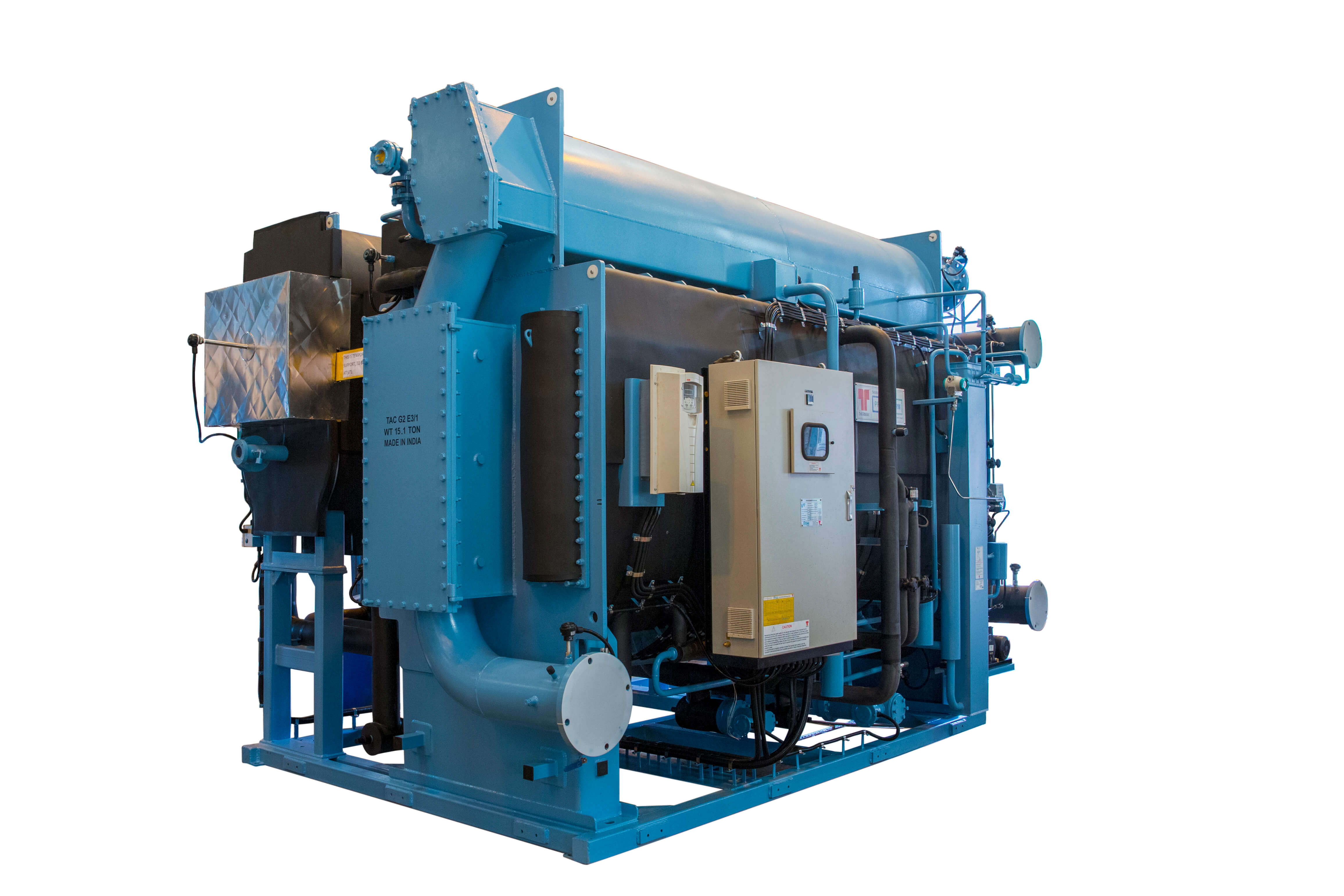
DOUBLE EFFECT DIRECT FIRED ABSORPTION CHILLER
Heat Source: Direct Fuel Firing
COP: 1.5
Capacity: 50 – 3000 TR
Heat energy available in the form of
- Natural gas
- LPG
- Propane
- Town gas
- Kerosene
- High speed diesel
- Oil
- Biogas
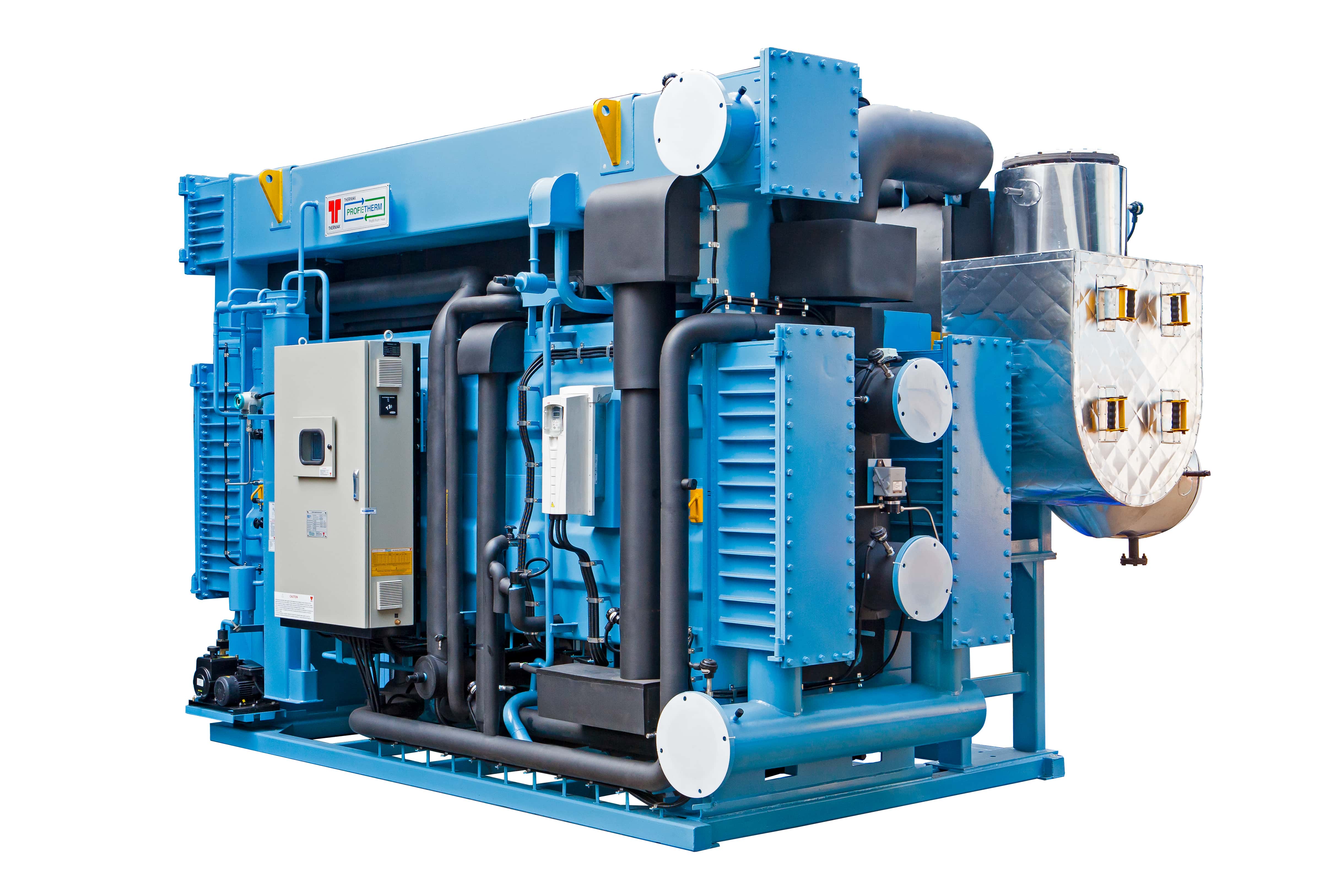
DOUBLE EFFECT EXHAUST FIRED ABSORPTION CHILLER
Heat Source: Exhaust Gas
Inlet Temperature: 250OC – 600OC
COP: 1.5
Capacity: 50 – 3500 TR
Heat energy available in the form of
- Flue gas from gas engines or diesel engines
- Flue gas from gas turbines
- Flue gas from micro turbines
- Flue gas from fuel cells
- Clean Flue gas from ovens, furnaces, thermic fluid heaters etc.
HIGH EFFICIENCY CHILLER – HEATER
Heat Source: Steam, Hot Water, Direct Fuel Firing & Exhaust Gas
Capacity:
Cooling : 100 – 3500 TR
Heating : 100 Kw – 9 MW
Heat energy available in the form of
- Dry saturated steam – 3.0 – 10.0 bar.g
- High temperature hot water -145 – 180OC
- Direct fuel firing – Gas / Oil / LPG / Propane)
- Exhaust gas (275 – 600OC)
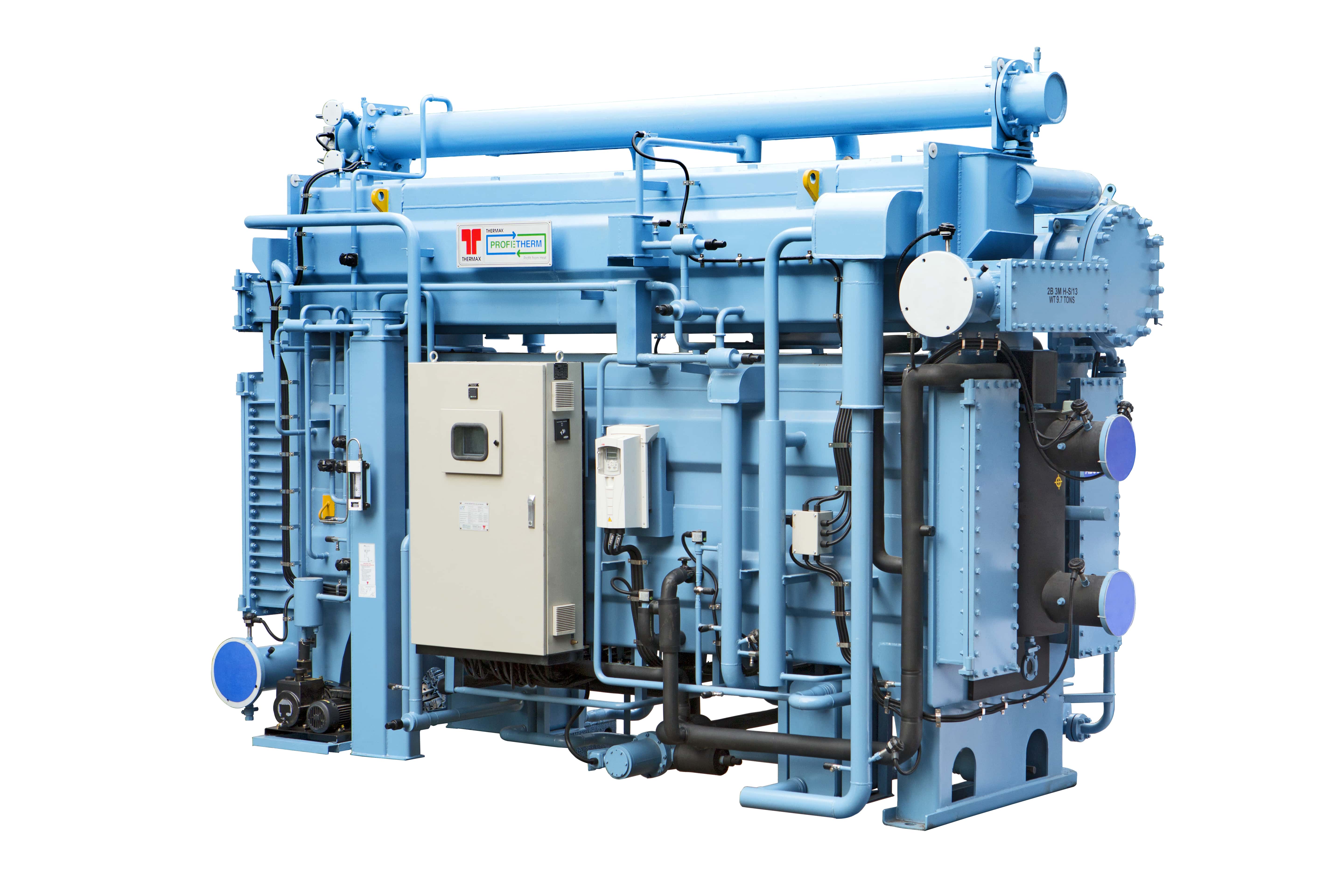
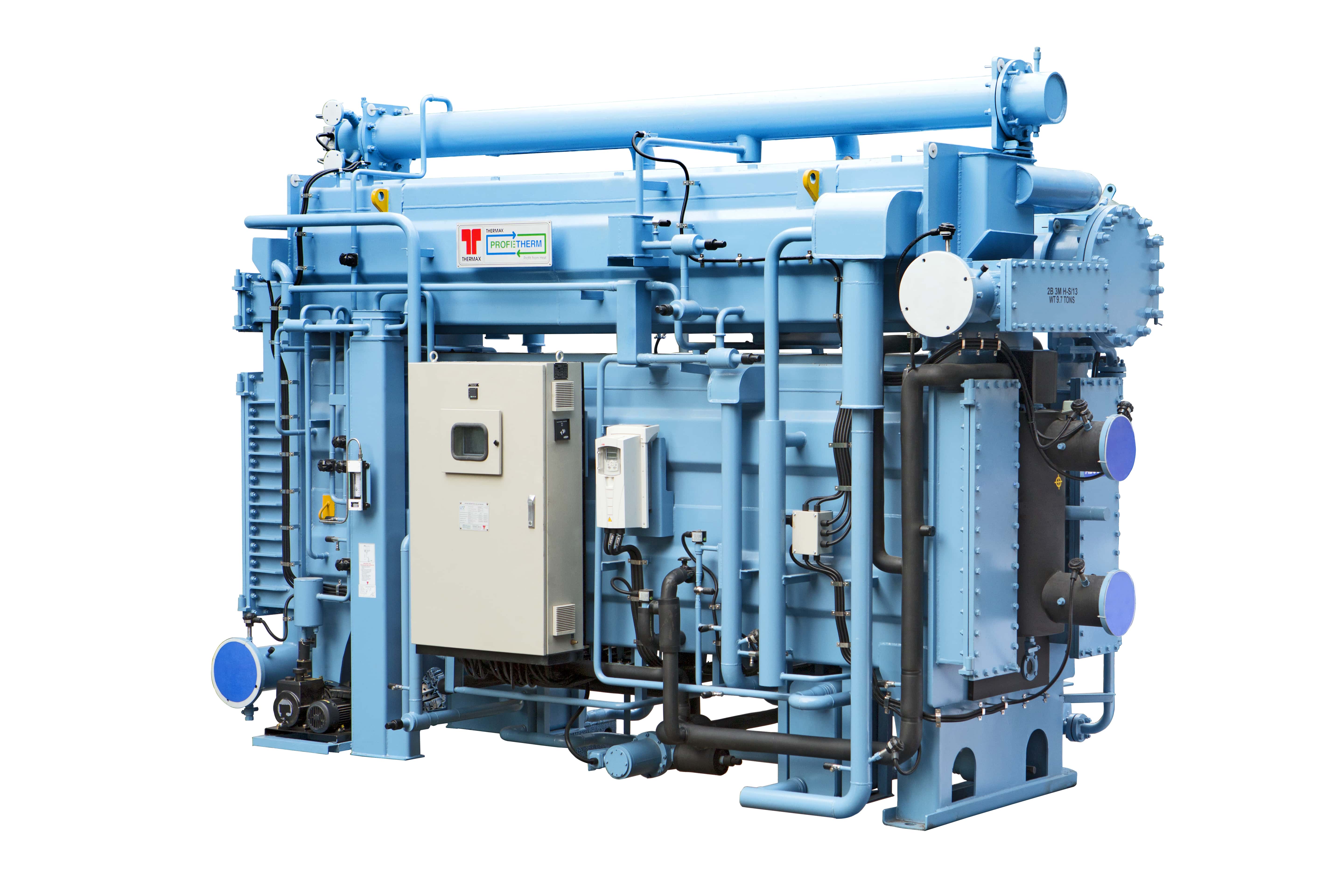
HIGH EFFICIENCY CHILLER – HEATER
Heat Source: Steam, Hot Water, Direct Fuel Firing & Exhaust Gas
Capacity:
Cooling : 100 – 3500 TR
Heating : 100 Kw – 9 MW
Heat energy available in the form of
- Dry saturated steam – 3.0 – 10.0 bar.g
- High temperature hot water -145 – 180OC
- Direct fuel firing – Gas / Oil / LPG / Propane)
- Exhaust gas (275 – 600OC)
REFERENCES
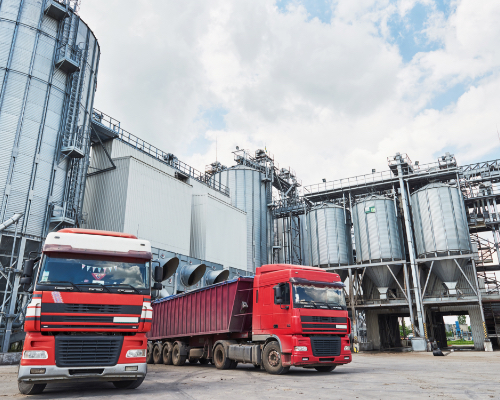
Godrej
Location: India
Type: Double effect steam fired absorption chiller
Capacity: 80 TR
No. of machine: 1
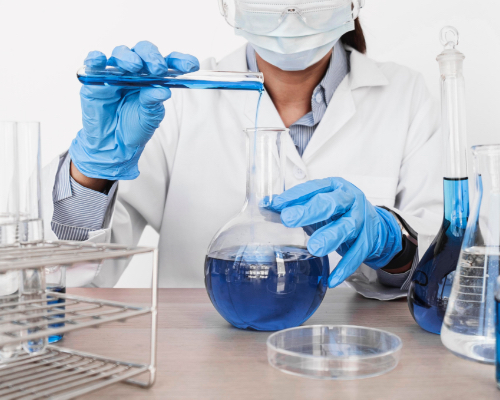
Deccan Fine Chemicals
Location: India
Type: Double effect steam fired absorption chiller
Capacity: 600 TR
No. of machine: 1
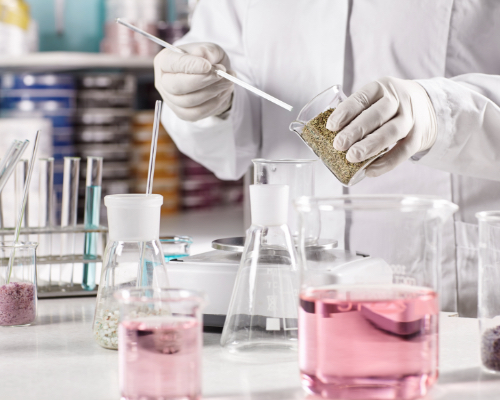
Grasim Industries Limited
Location: India
Type: Low temperature hot water driven absorption chiller
Capacity: 140 TR
No. of machine: 1
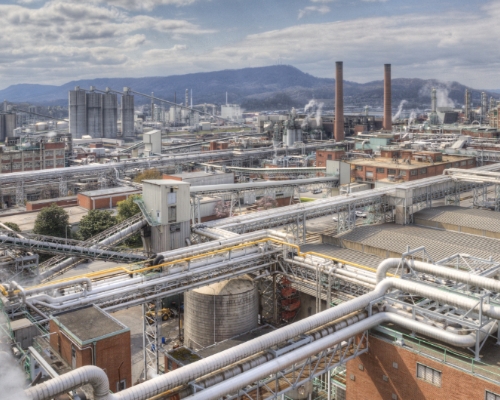
Eastman Chemical Company
Location: USA
Type: Single effect steam fired absorption chiller
Capacity: 1400 TR
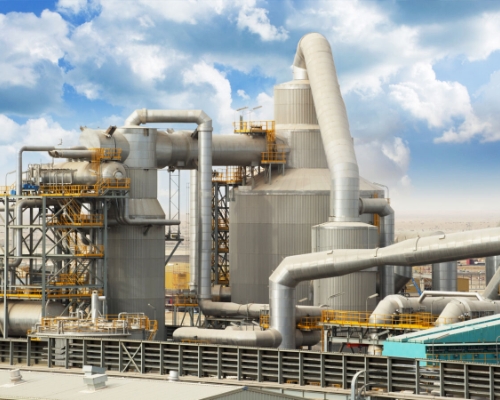
Eti Bakir
Location: Turkey
Type: Double effect steam fired absorption chiller
Capacity: 529.1 TR
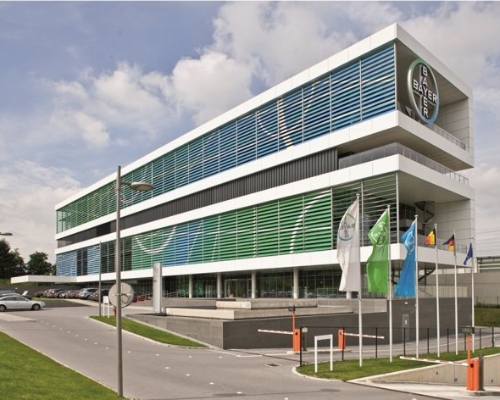
Bayer Material Science
Location: USA
Type: Single effect steam fired absorption chiller
Capacity: 1490 TR