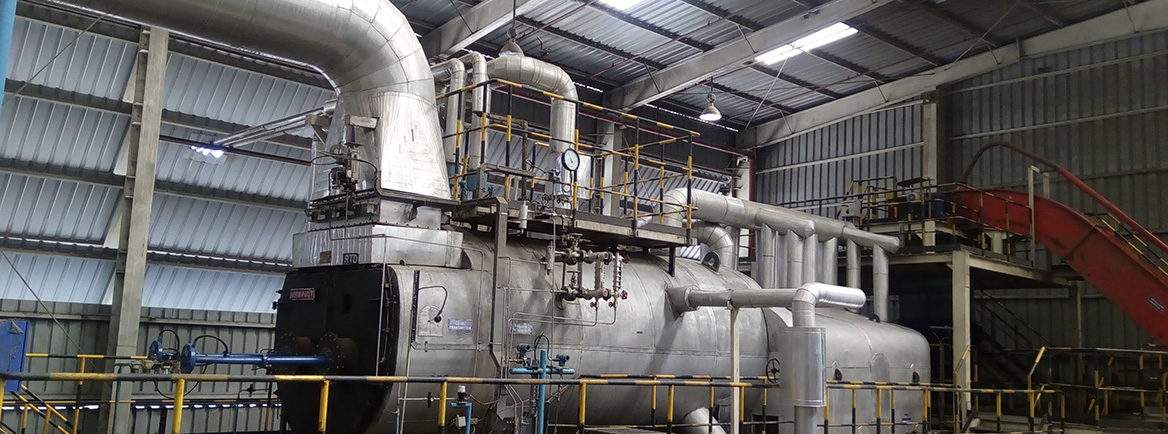
Thermax supports ITC’s green initiative by offering 100% biomass-fired boiler ensuring cost saving up to 45%
Introduction
Our legacy is enriched with the green effect projects for which we are the first choice for some of the global brands in the word. ITC Group which holds a market capitalization of 50 billion USD with a turnover of 8 billion USD crediting to their robust portfolio of traditional and Greenfield businesses is one such esteemed business alliance for Thermax process heating solutions.
The multi-business conglomerate encompasses various manufacturing plants across India and one of them is at Ranjangaon, Pune MH. This food production unit manufactures instant noodles and potato chips. A heating system is the heart of any food processing unit and ITC group partnered with Thermax for a robust heating system. ITC group’s association with Thermax was cemented with the commitment to supply a
Project Insights
In 2012 ITC was looking for expansion and was keen to have a greener, cost-effective fuel, they decided to go for 100% biomass briquettes fired boiler from Thermax. There were three main criteria’s for this project – 1) Uninterrupted steam supply, 2) fast response to fluctuating load and 3) high efficiency. As ITC was keen to have 100% biomass-fired unit the biggest challenge was maintaining steam-fuel ratio as the calorific value of fuel i.e. biomass briquettes changes drastically due to the variation in moisture content, bulk density, ingredients of briquettes etc. Thermax understood customer’s requirement and proposed a fully automatic CPRG (Combipac Reciprocating Grate) boiler with automatic fuel feeding system, air pre-heater, and economizer to ensure best in class efficiency with suitable equipment.
Innovative solution by Thermax
Reciprocating grate
Energy efficient and low emission operation
Positive impact
The flue gas exit temperature is at 100-120° C. The boiler achieves SFR of 5 and ash percentage is as low as 14-15%. The SPM level is as low as 28 ppm. In order to achieve optimum fuel consumption, an O2 controller is integrated into the plant. An oxygen probe measures oxygen continuously and compensates changes in air temperature and air pressure automatically. This optimizes the efficiency of the boiler and reduces the negative environmental impact at the same time.
Continues automation and reliability
The high degree of automation in the steam boiler plant provides comfort and safety to the boiler operator who can see complete process of the boiler from a system linked computer screen. The controller can also manage the equipment and other parameters like fuel feeding, feed water section, combustion manager, and flue gas section, making the boiler unit an automated, timely and reliable solution. This makes the entire plant operation automated and the process can be managed by limited no of people.
The result