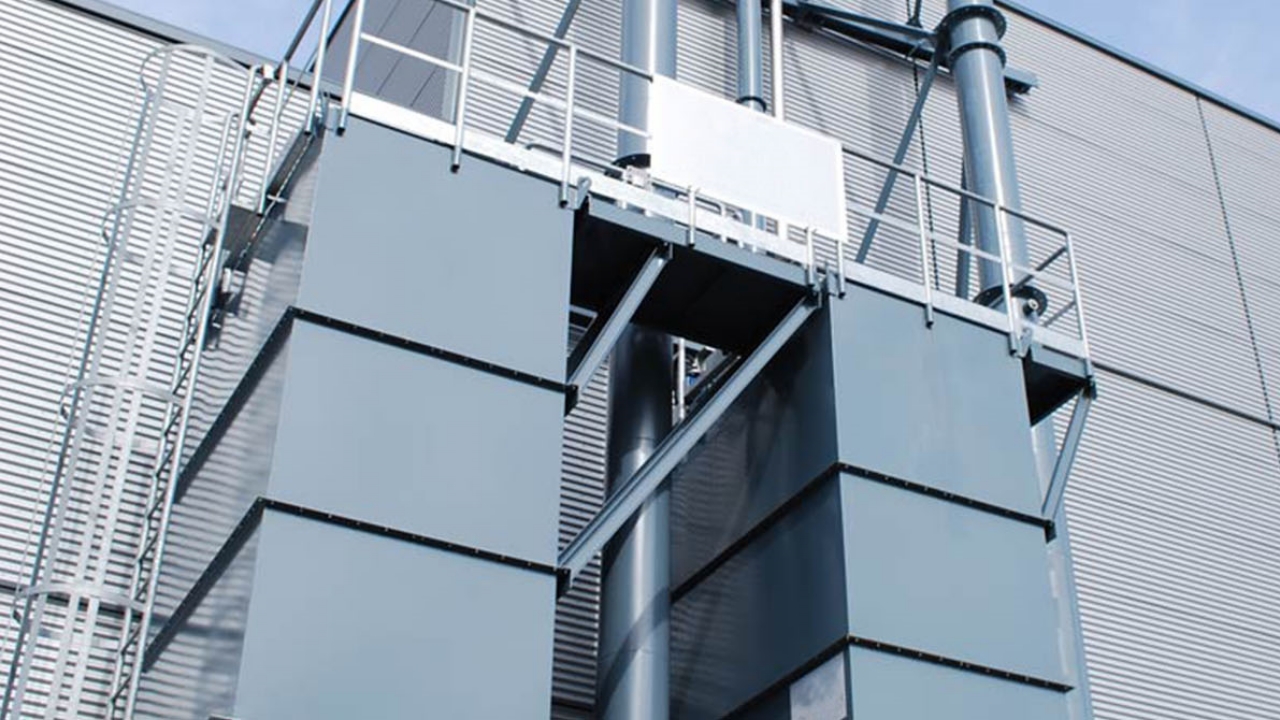
INTRODUCING THERMAX’S PATENTED PULSING SYSTEM, AN INNOVATIVE WAY TO IMPROVE BAG FILTER PERFORMANCE
INTRODUCTION
The shrinking profit margins and fierce competition coupled with increased taxes and higher logistics cost has compelled the cement manufacturers to reduce operating expenses and increase throughput without allocating considerable CAPEX.
This has led the Cement Manufacturers as well as Equipment Suppliers to look out for solutions which will yield maximum equipment efficiency enabling higher throughput of the existing plant. Thermax has acknowledged the market requirement and introduced a patented pulsing system that improves the bag filter performance in an innovative way. The success story of Thermax’s innovative solution to address the needs of the cement industry is presented below:
THE CASE
Myhome Cement, Hyderabad approached Thermax for a solution to upgrade its existing cement mill bag house to increase its mill feed capacity from 175TPH to 220TPH. However, increasing its capacity in as is condition was notpossible since the existing Induced Draft (will be referred to as ID henceforth) Fan of Cement Mill had flow & static pressure limitations due to higher pressure drop/ losses in system. The data in Table 1 presents the input parameters for existing operation and future enhancement:
Sr. No. | Description | Slag/Clinker Grinding Mill Bag Filter – Existing (Design Data) | Slag/Clinker Grinding Mill Bag Filter – Enhanced (Design Data) |
1. | Cement Mill Bag filter | Online | Online |
2. | Quantity | 1 | 1 |
3. | Industry | Cement | Cement |
4. | Application | Slag/Clinker Mill Filter | Slag/Clinker Mill Filter |
5. | Mill Feed, TPH | 175 | 220 (21% increase desired after Mill upgrade) |
6. | Volumetric flow | 5,95,000 Am3/hr | 7,00,000 Am3/hr (15% increase, desired) |
7. | Gas temperature continuous | 90°C | 90°C |
8. | Max Gas temperature Bags can Withstand | 130°C | 130°C |
9. | Bag Filter Design Pressure | +/- 1500 mmwg | +/- 1500 mmwg |
10. | Static pressure at Bag Filter inlet (max) | (-)450mmwg | (-)450mmwg |
11. | Dust to be handled | Slag / Clinker Dust | Slag / Clinker Dust |
12. | Dust properties | Abrasive, Free Flowing | Abrasive, Free Flowing |
13. | Dust concentration in the gas at Inlet of bag filter (slag only) | 248 gms/m3 | 257 gms/m3 300 gms/m3(max) |
14. | Outlet Emission | 30 mg/Nm3 | 30mg/Nm3 |
15. | Bulk density of dust for Power | 1,200 kg/m3 | 1,200 kg/m3 |
16. | Particle Size Analysis | 4,200 Blains | 4,200 Blains |
17. | Moisture content in the gas | Upto 8% | Upto 8% |
18. | Moisture dew point of gas | 59°C max | 59°C max |
THE CHALLENGES
Higher CAPEX
- Generally, this kind of bag filter upgrade calls for an increase in the number of filter bags/ modules, to maintain air-to-cloth ratio (will be referred to as ACR henceforth) by increasing the fabric collection area and to maintain the Differential Pressure (will be referred to as DP
henceforth) across the system - Any rework in an existing plant requires a lot of re-routing of existing facilities, in order to accommodate extra filter bags/modules. This results in increased expenditure for the customer
Space constraints
Space constraint was a challenge due to a compact plant layout and hence no space to accommodate additional bag filter modules.
Revenue loss due to downtime
Longer downtime required for addition of the bags/module resulting in loss of production and revenue accordingly
THE SOLUTION
INNOVATIVE PULSING SYSTEM
Thermax’s state-of-the-art Research, Technology and Innovation center (RTIC) has developed an innovative bag filter pulsing system which can effectively dislodge dust from bags at low pressures resulting in effective control of bag filter DP and ensure higher bag life. In fact, this also addresses the challenge of effective cleaning of long bags. The system generates low pressure pulses which travel right up to the bottom of the bag causing ripple effect on the bags and effectively dislodging dust, a panacea for cement
manufacturer’s plant operations woes.
The picture below represents the Computational Fluid Dynamics (CFD) pattern for Pulse Cleaning System; Type C is Thermax’s Intellectual Property (IP).
RESULTS
Sr. No. | Parameters for 100% Slag Grinding | Case 1 With Old Pulsing System | Case 2 With Improved Pulsing System | Case 3 With Improved Pulsing System |
1. | Mill Feed | 175 – 180 | 175 – 180 | 185 – 190 |
2. | Flow, m3/hr | 5,65,000 – 5,80,000 | 5,65,000 – 5,80,000 | 7,05,000 – 7,15,000 |
3. | Fan, RPM | 800 – 810 | 800 – 810 | 980, Full RPM |
4. | Fan Power, KW | 1,180 – 1,190 | 1,175 – 1,185 | 2,120 – 2,150 |
5. | Pulsing Pressure, Bar | 5 – 6 | 3.8 – 4.2 | 3.8 – 4.5 |
6. | DP across Bag Filter, mmwg | 90 – 100 | 70 – 80 | 115 – 120 |
7. | Emission | 30 mg/Nm3 | 30 mg/Nm3 | 30 mg/Nm3 |
8. | Bag House Inlet/outlet Temp., °C | 117 / 103 | 117 / 105 | 118 / 99 |
(*) Enhanced mill feed capacity of 220TPH was not achieved with old pulsing system due to very high DP across
bag house.
Thermax innovative pulsing system achieved 24% to 30% drop in pulsing pressure and 20% to 22% drop in DP
across bag filter (as in Case 2, Table 2)
The Mill Feed throughput was increased to 190 tph, but desired figure of 220 tph is yet to happen. However, the air flow in the bag filter was increased to 7,00,000 m3 /hr equivalent to 220 tph for couple of hours to observe the DP value under full load. The DP was around 115 – 120 mmwg while the original Bag Filter DP (design value) = 150 mmwg.
The above case clearly illustrates the benefits of the improved pulsing system i.e., reduced DP, reduced compressed air requirements, increased throughputs and higher bag life.
The set of benefits realised by customer (Myhome Cement) due to innovative pulsing system in an existing cement mill bag filter:
1. Savings in electric power consumption of ID fan:
Reduction of 20mmwg in dp across Bag Filter (Table 2, Case-1 & 2) would convert to 5KWH which would mean a yearly saving of 5KWH x 8,000 x Rs.5* per KWH = Rs. 2,00,000 (Rs.5 per KWH – Ave. India Industrial Unit Rate)
2.Savings in compressed air power consumption:
Reduction in pulse pressure from 5 – 6 kg/cm2 to 3.8 – 4.2 kg/cm2 , means a net reduction by 24% to 30% in air compressor operating expenses
3.Saving due to extended bag life:
Apart from other governing factors, compressed air pulse pressure and pulse frequency plays an important role in the life cycle of bag house. The innovation in the pulsing system technology by Thermax has controlled these vital parameters to safeguard the cement manufacturers from frequent purchase of bags translating into lower operating expenses
4.Saving due to pulsing system up gradation vis-à- vis additional module integration:
Conventional approach for DP reduction is reduction in ACR which would mean increase in module size. As against this, upgrading to new pulsing system would mean savings to the tune of 80 – 85% of capital cost. In addition, there is downtime reduction and intangible saving in terms of space.
CUSTOMER FEEDBACK
Thermax was referred for studying the possibility to control higher DP across the bag house, during change in operation of bag house fan from 810-820 RPM (Results: Case 1) to higher speed of 960-980 RPM (Results: Case 3), for improving the mill throughput.
Instead of increasing the modules in the bag house, Thermax Team has modified pulsing system to reduce the DP in higher ID fan RPM operation. The modified pulsing system was installed and observed for the DP reduction from 85 – 95 mmwg to 65 – 75 mmwg and pulse air pressure reduced from 5 – 6 kg/cm2 to 3.8 – 4.2 kg/cm2.
“We appreciate Thermax for their support for solving the DP problem and overall savings in power cost in terms of DP reduction & Compressor Air Pressure reduction,” said Mr. Narang, MyHome Cement, Hyderabad.
Authored by
Mr. Arijit Dutta
Head of Innovation and Service Business Group
Thermax Limited | Air Pollution Control