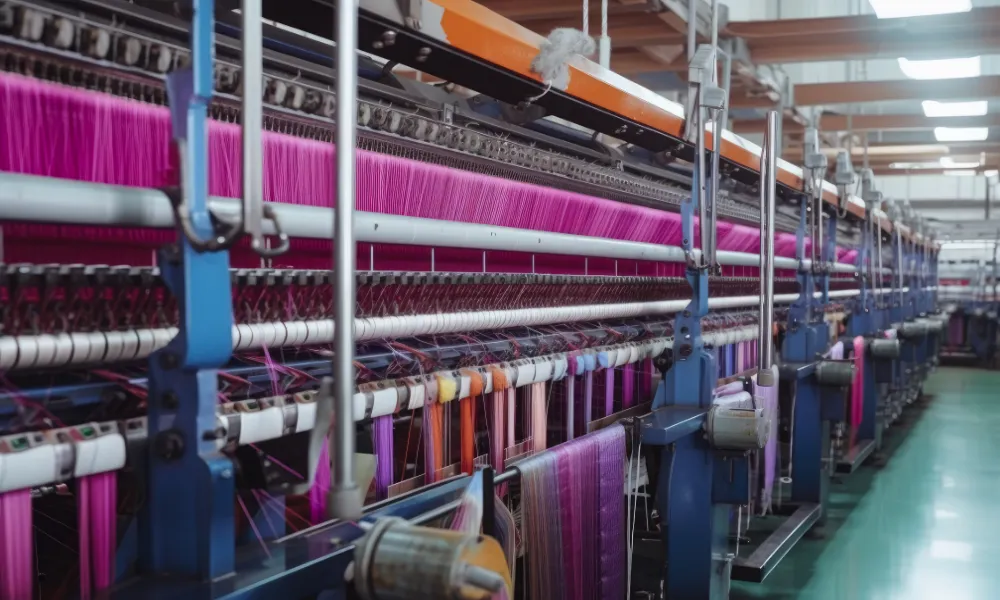
Navigating Energy Transition: Comprehensive Solutions for Textile Players in the Pursuit of Sustainability
In the vibrant tapestry of India’s economy, the textile industry emerges as a potent force, weaving not just fabric but also millions of livelihoods. More so, India has a 4% share of the global trade in textiles and apparel. Yet, amidst this growth, there is a silent concern – the conventional methods and materials integral to the textile processes that often impact the environment negatively.
From dyeing practices to energy-intensive operations like spinning and weaving, the industry’s ecological footprint demands reconsideration. As India progresses on its sustainable endeavours, it is a rallying call for textile players to steer their course towards cleaner, more responsible technologies. Thermax stands poised to facilitate this transformation with its repertoire of solutions, services, and custom-tailored innovations designed to steer the textile sector towards a greener future.
At the heart of textile manufacturing lies the heating systems, historically based on fossil fuels, emanating emissions that corrode the environment. Thermax offers a spectrum of heating solutions that empower textile manufacturers to adopt renewable energy alternatives viz. renewable power, biomass, waste-to-energy, and innovative waste heat recovery. These solutions can lead to lower emissions and a more environmentally friendly approach.
Consider the case of a textile manufacturing facility in Pune, Maharashtra grappling with the dual burdens of high energy costs and excessive carbon emissions due to oil consumption. Thermax Onsite Energy Solutions Limited (TOESL) stepped in offering a biomass-fired boiler, introducing the ‘Build-Own-Operate’ model. The result was a remarkable reduction in operational costs, lowered carbon footprint, and a steadfast boiler performance – a notable achievement towards sustainability without any upfront investment.
Thermax’s impact does not halt within borders. Thermax’s steam fired vapour chillers provide cooling to an aged textile plant in Bangladesh. Understanding that energy significantly affects operational expenses, Thermax conducts energy audits to analyse consumption patterns. These audits uncover inefficiencies and provide customised solutions to optimise energy usage, resulting in more efficient operations, increased productivity, and a greener footprint.
Thermax’s expertise involves capturing and utilising the excess heat produced during textile production, reducing energy needs and dependence on fossil fuels. In addition to energy efficiency, Thermax also addresses water treatment and wastewater management challenges. This holistic approach ensures a circular water usage cycle, alleviating stress on limited water resources and averting pollution.
A notable milestone is the Zero Liquid Discharge plant in Ambasamudram, Tamil Nadu, which displays Thermax’s commitment. This plant includes an effluent treatment unit, a recycling facility, and advanced evaporators, contributing to a zero-waste goal that echoes Thermax’s promise to protect the environment.
The journey doesn’t stop here. Thermax’s legacy in the textile industry burgeons with a commitment to spearheading a transition towards cleaner, sustainable practices. It is a steadfast partnership, spanning diverse regions and resonating with the vision of an energy-conscious world.
For enquiries related to clean air, clean energy and clean water solutions, reach out to us at enquiry@thermaxglobal.com or call us at 1800-209-0115.