PHARMACEUTICAL INDUSTRY
Thermax’s cooling and heating solutions help achieve regulatory and sustainability goals of pharmaceutical industries with unique means of operation
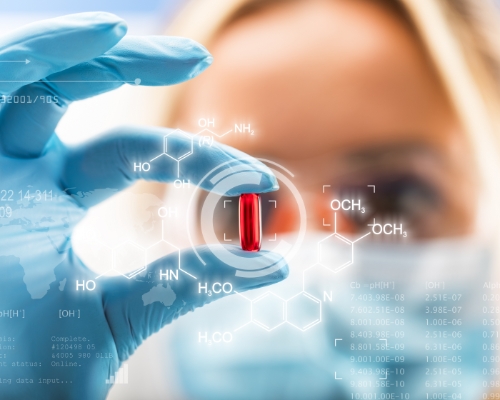
In light of the rising energy costs and need for sustainability, energy optimisation remains the priority of pharmaceutical industry. Pharma manufacturers heavily rely on cooling solutions for humidity control and process cooling. Conventional cooling utilities are energy-intensive and hence account for a huge portion of the industry’s energy use. Thermax’s cooling solutions can meet the cooling requirements effectively at lower energy costs and reduce the associated emissions.
Thermax’s cooling solutions find application in
- Bulk drug production
- Reactor cooling
- HVAC / AHU application
- Primary condenser of distillation column
- Secondary condenser of distillation column
- Solvent recovery
- Refrigeration
- Water Treatment
- Air Handling Unit
Pharma facilities have Air Handling Units (AHU) for dehumidification of ambient air. Chilled water pumped into the AHU enables heat exchange and helps in maintaining humidity and temperature within the facility.
- Solvent Recovery
Cooling tower water or chilled water condenses vapours in solvent recovery units and hence facilitates higher recovery rates of the pharmaceutical product.
- Clean Rooms
Clean rooms in pharma require optimal temperature and humidity in to avoid bacterial growth. Chilled water aids in keeping the room sterile.
- Refrigeration
Given the extremely high value of pharmaceutical raw materials, intermediates and finished products, refrigeration systems in their plants are vital.Evaporative condenser fits in as a precise cold storage system for pharma with very high reliability.
- Water Treatment
Conventional cooling tower uses evaporation to reduce process water temperature. Closed-loop Cooling Tower (CLCT) uses ambient air to cool the water resulting in reduced water consumption and energy costs.
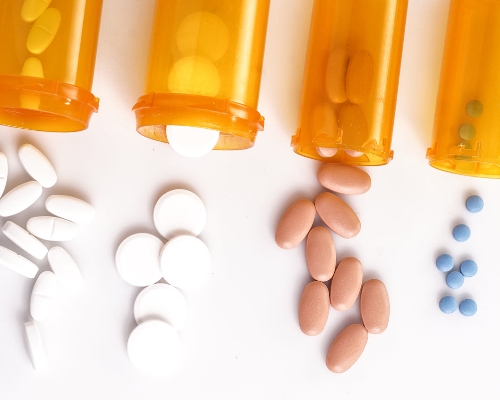
BENEFITS
- Heat recovery
- Reduce operational costs
- Zero contamination
- Water savings
- Lower emissions
To know more about the application and benefits of our solutions, contact our experts now
OUR OFFERINGS
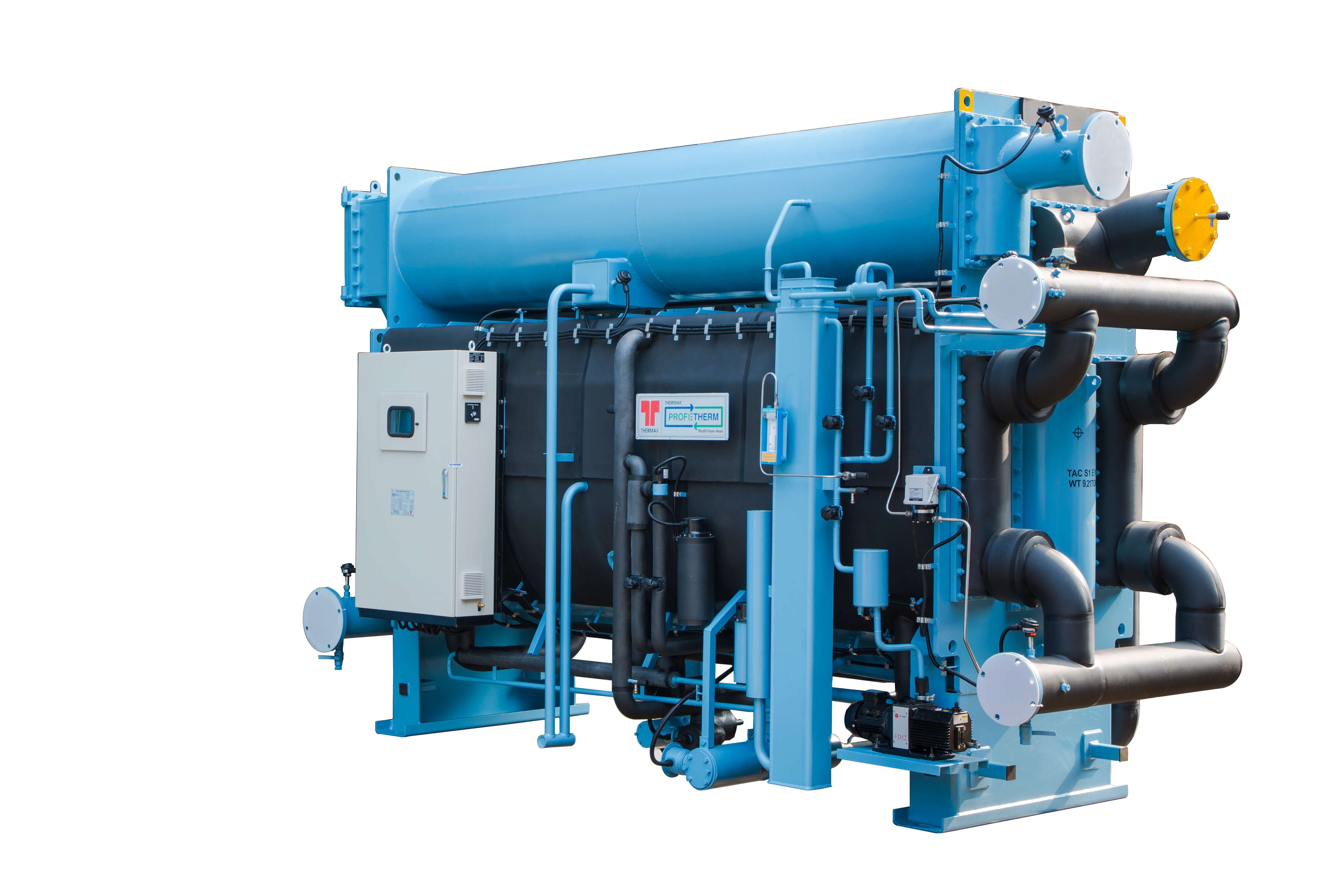
SINGLE EFFECT STEAM DRIVEN VAPOUR ABSORPTION CHILLER
Heat Source: Steam
Pressure: 0 bar.g – 3.5 bar.g
COP: 0.8
Capacity: 100 – 3500 TR
Heat energy available in the form of (LP- low pressure)
- LP vapour (0.1 bar.g, 103OC) coming from continuous polymerisation process in textile industry
- LP steam generated from potato fryer, instant noodle plant etc.
- LP Steam extraction from steam turbine in power plants
- Flash steam recovery
SINGLE EFFECT LOW TEMPERATURE HOT WATER DRIVEN VAPOUR ABSORPTION CHILLER
Heat Source: Hot Water
Inlet water temperature: 80OC – 120OC
COP: 0.8
Capacity: 180 – 1650 TR
Heat energy available in the form of
- Engine jacket water
- Hot water from solar collectors
- Process condensate
- Flue gas recovery from incinerators
- Process heat recovery
- Fuel cells
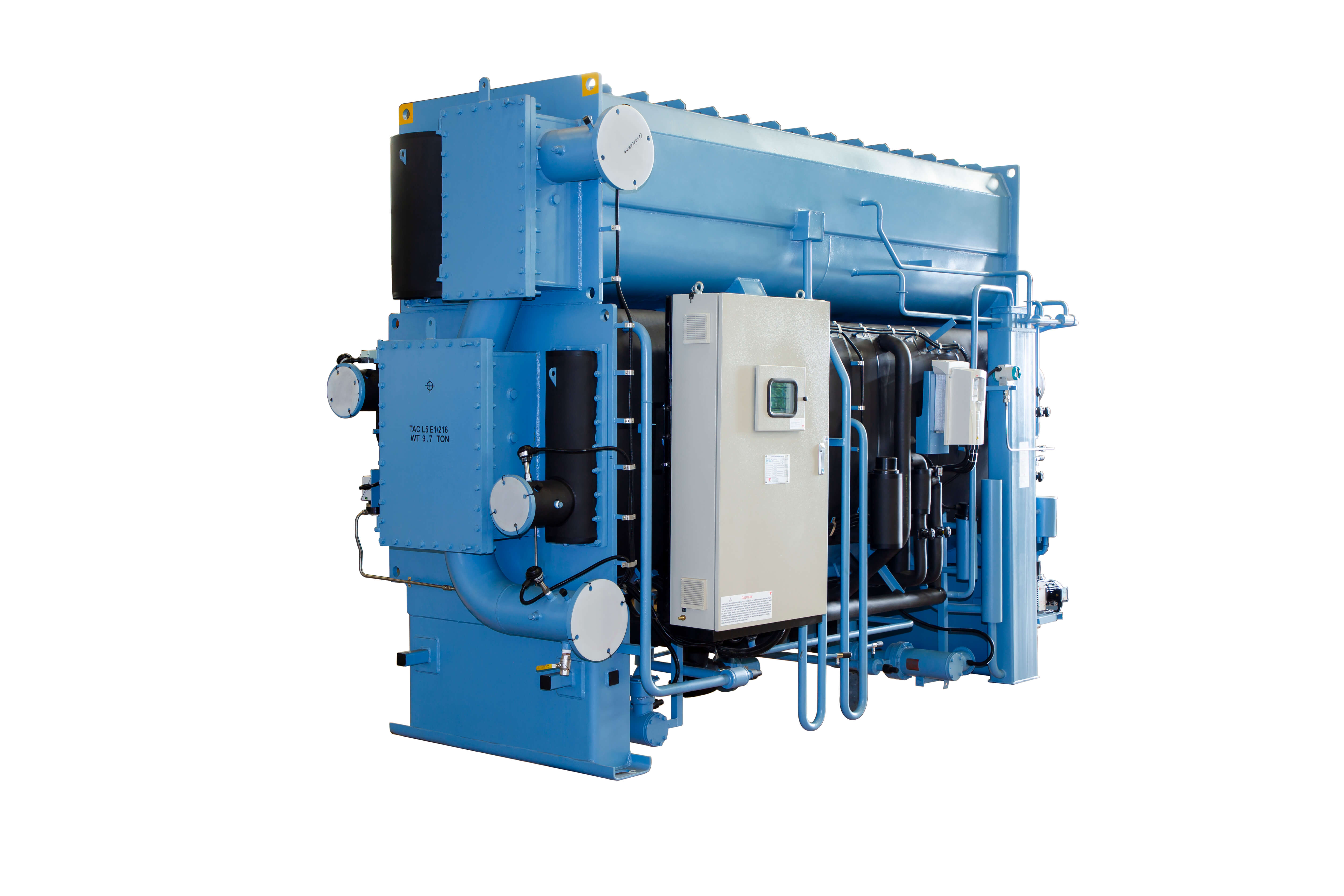
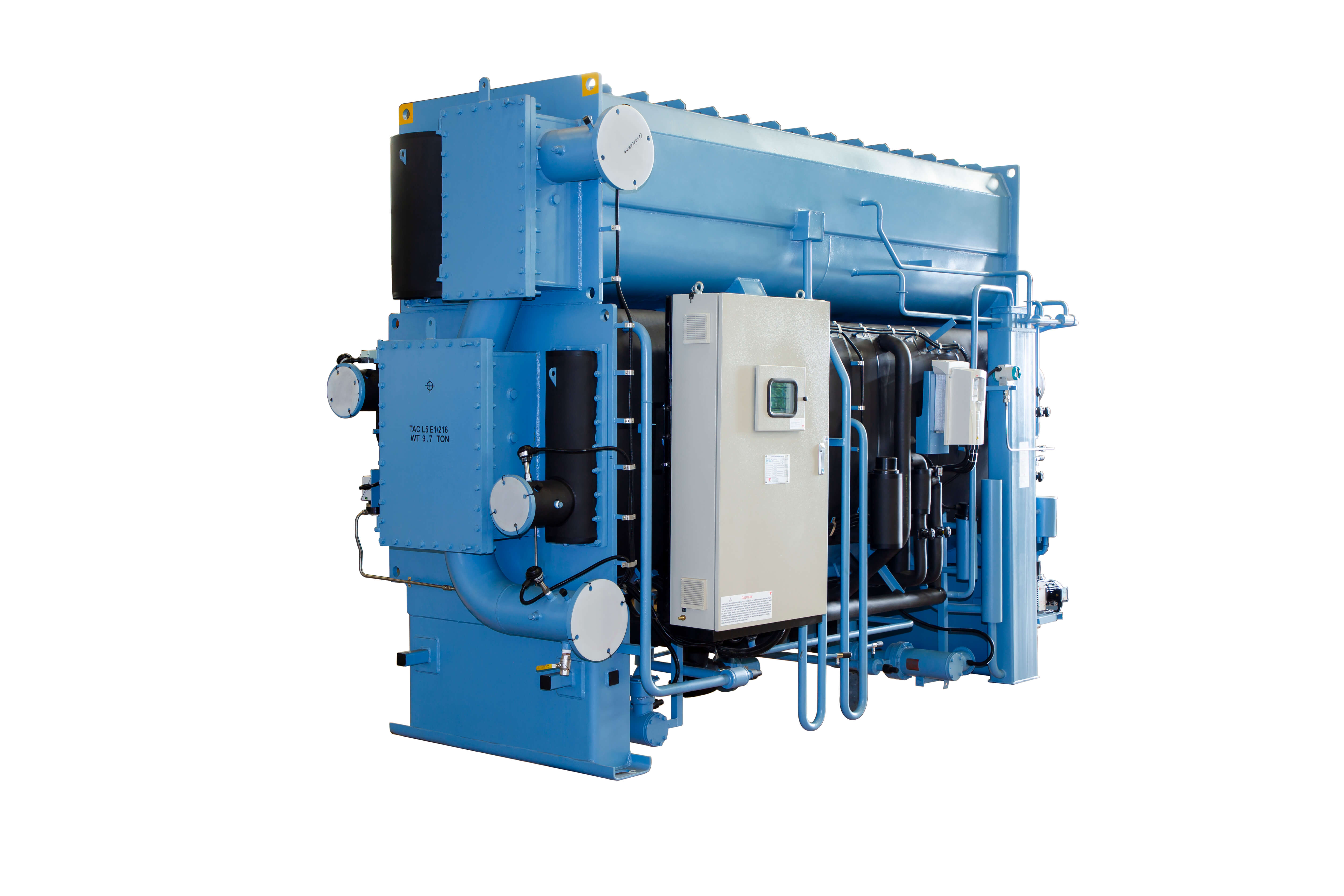
SINGLE EFFECT LOW TEMPERATURE HOT WATER DRIVEN VAPOUR ABSORPTION CHILLER
Heat Source: Hot Water
Inlet water temperature: 80OC – 120OC
COP: 0.8
Capacity: 180 – 1650 TR
Heat energy available in the form of
- Engine jacket water
- Hot water from solar collectors
- Process condensate
- Flue gas recovery from incinerators
- Process heat recovery
- Fuel cells
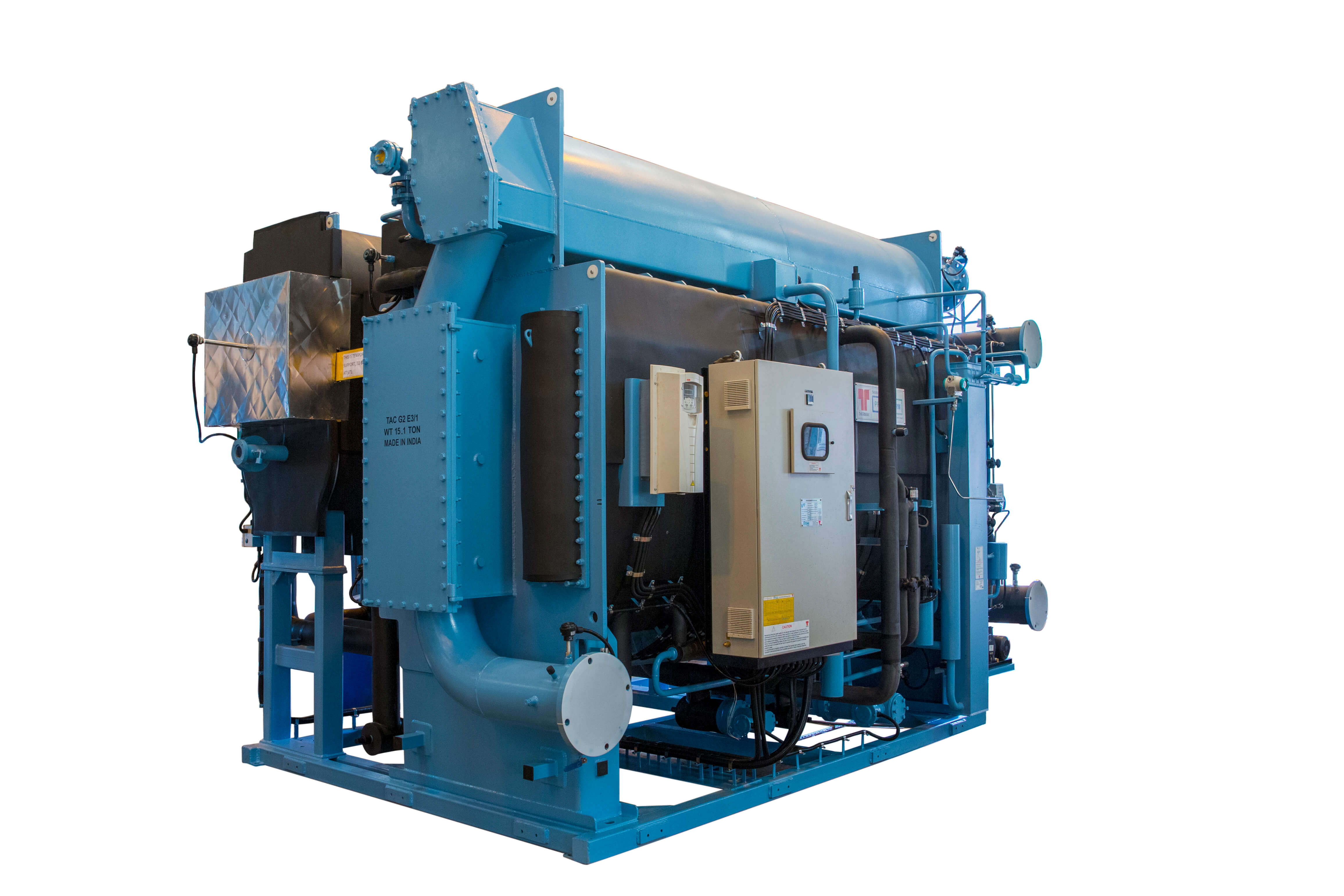
DOUBLE EFFECT DIRECT FIRED ABSORPTION CHILLER
Heat Source: Direct Fuel Firing
COP: 1.5
Capacity: 50 – 3000 TR
Heat energy available in the form of
- Natural gas
- LPG
- Propane
- Town gas
- Kerosene
- High speed diesel
- Oil
- Biogas
HIGH EFFICIENCY CHILLER – HEATER
Heat Source: Steam, Hot Water, Direct Fuel Firing & Exhaust Gas
Capacity:
Cooling : 100 – 3500 TR
Heating : 100 Kw – 9 MW
Heat energy available in the form of
- Dry saturated steam – 3.0 – 10.0 bar.g
- High temperature hot water -145 – 180OC
- Direct fuel firing – Gas / Oil / LPG / Propane)
- Exhaust gas (275 – 600OC)
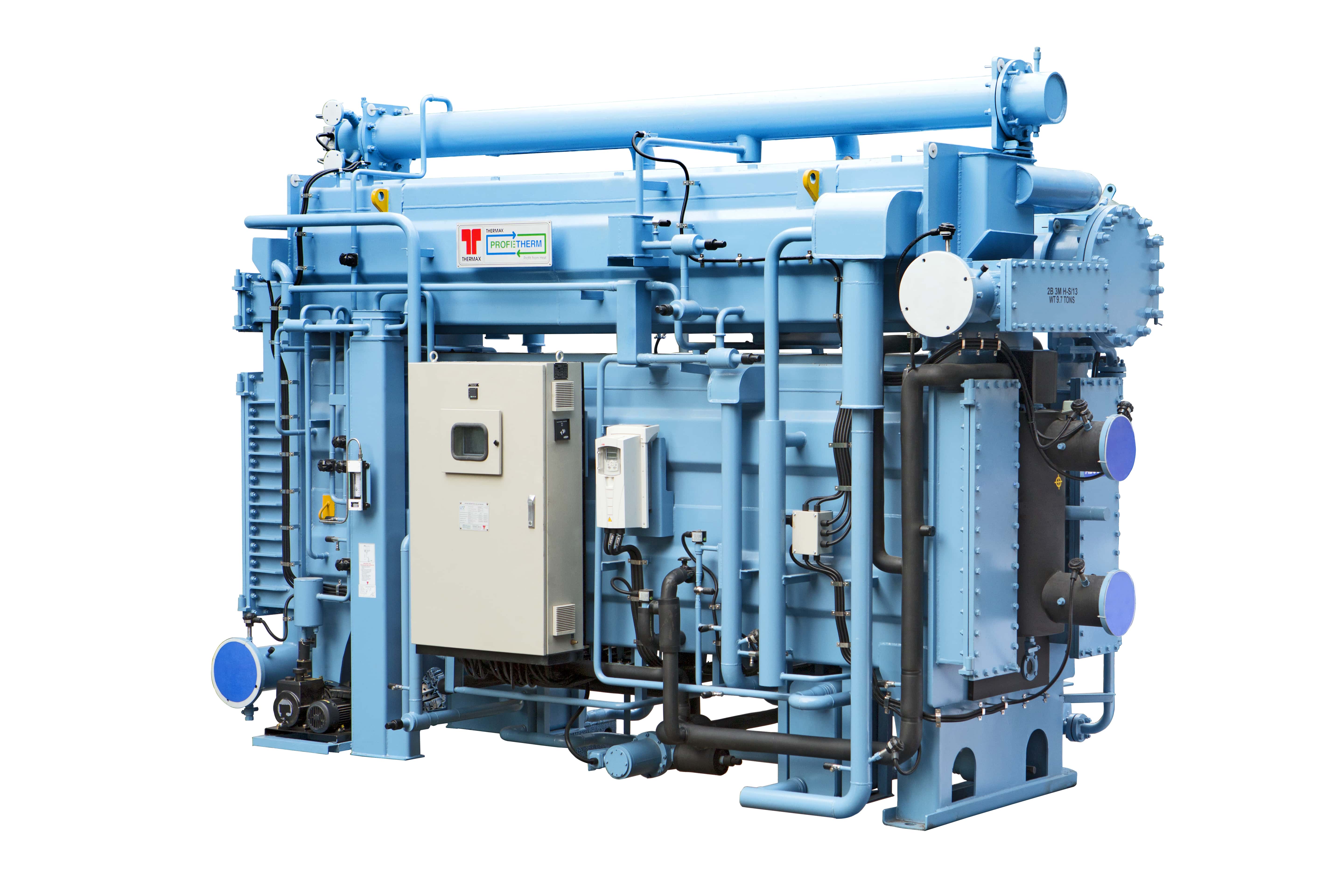
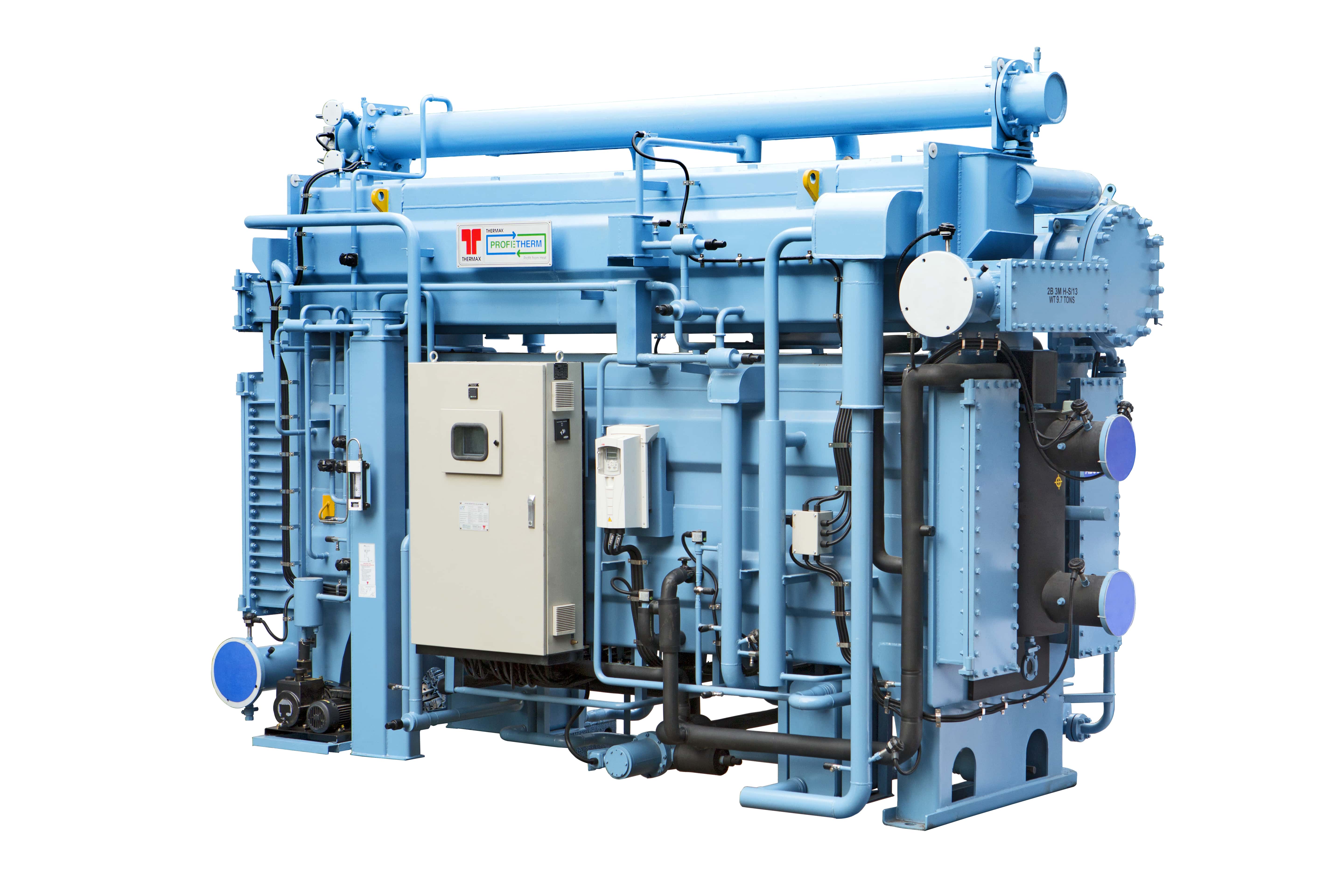
HIGH EFFICIENCY CHILLER – HEATER
Heat Source: Steam, Hot Water, Direct Fuel Firing & Exhaust Gas
Capacity:
Cooling : 100 – 3500 TR
Heating : 100 Kw – 9 MW
Heat energy available in the form of
- Dry saturated steam – 3.0 – 10.0 bar.g
- High temperature hot water -145 – 180OC
- Direct fuel firing – Gas / Oil / LPG / Propane)
- Exhaust gas (275 – 600OC)
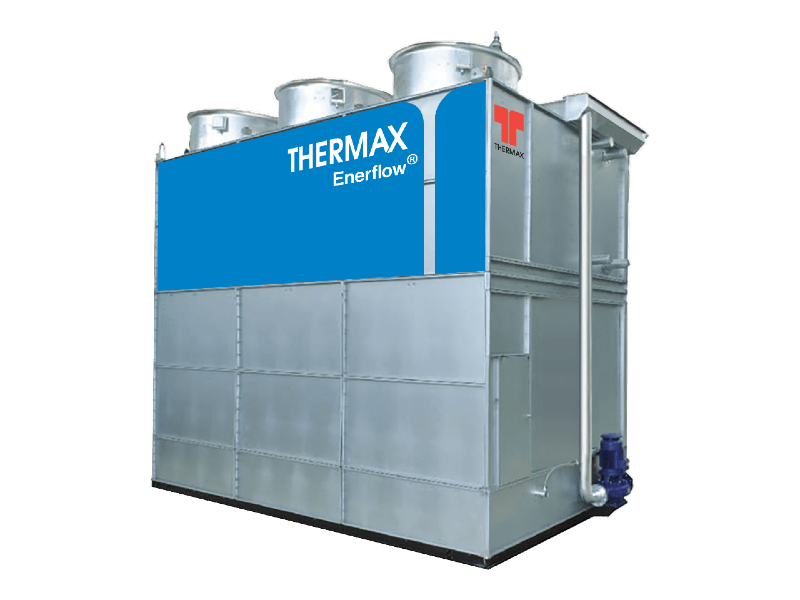
CLOSED LOOP COOLING TOWER
Product Features
- Can be operated for higher temperature difference (Δ T)
- Zero contamination due to closed loop
- 100% Water savings in exhaust steam condensing
- Low Maintenance Costs
- Lesser environmental impact due to the elimination of water los
Capacity: 20 m3/h onwards
EVAPORATIVE CONDENSER
Product Features
- Replacement product against conventional systems (atmospheric condenser, shell & tube heat exchanger + cooling tower, plate heat exchanger + cooling tower)
- For ammonia/freon condensation at lower temperature
- Ideal for various refrigeration systems and climatic conditions
- Compatible with all types of refrigeration compressors i.e. reciprocating, screw, scroll, rotary and centrifugal
- Combined and counter flow technology available
- Modular construction allows plug & play installation for new and replacement units
Product Capacity: 50 TR and above
Capacity: 20 m3/h onwards
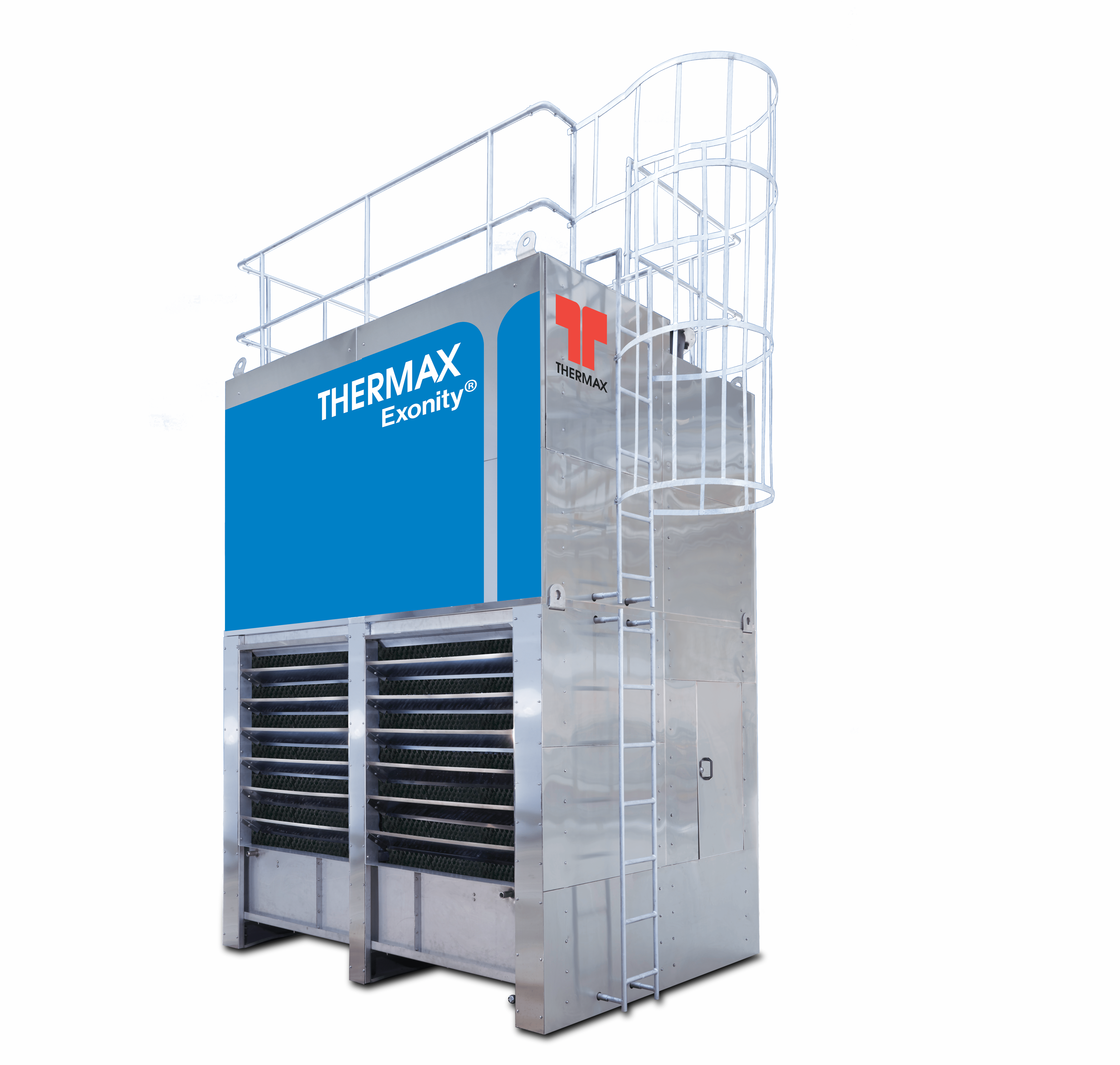
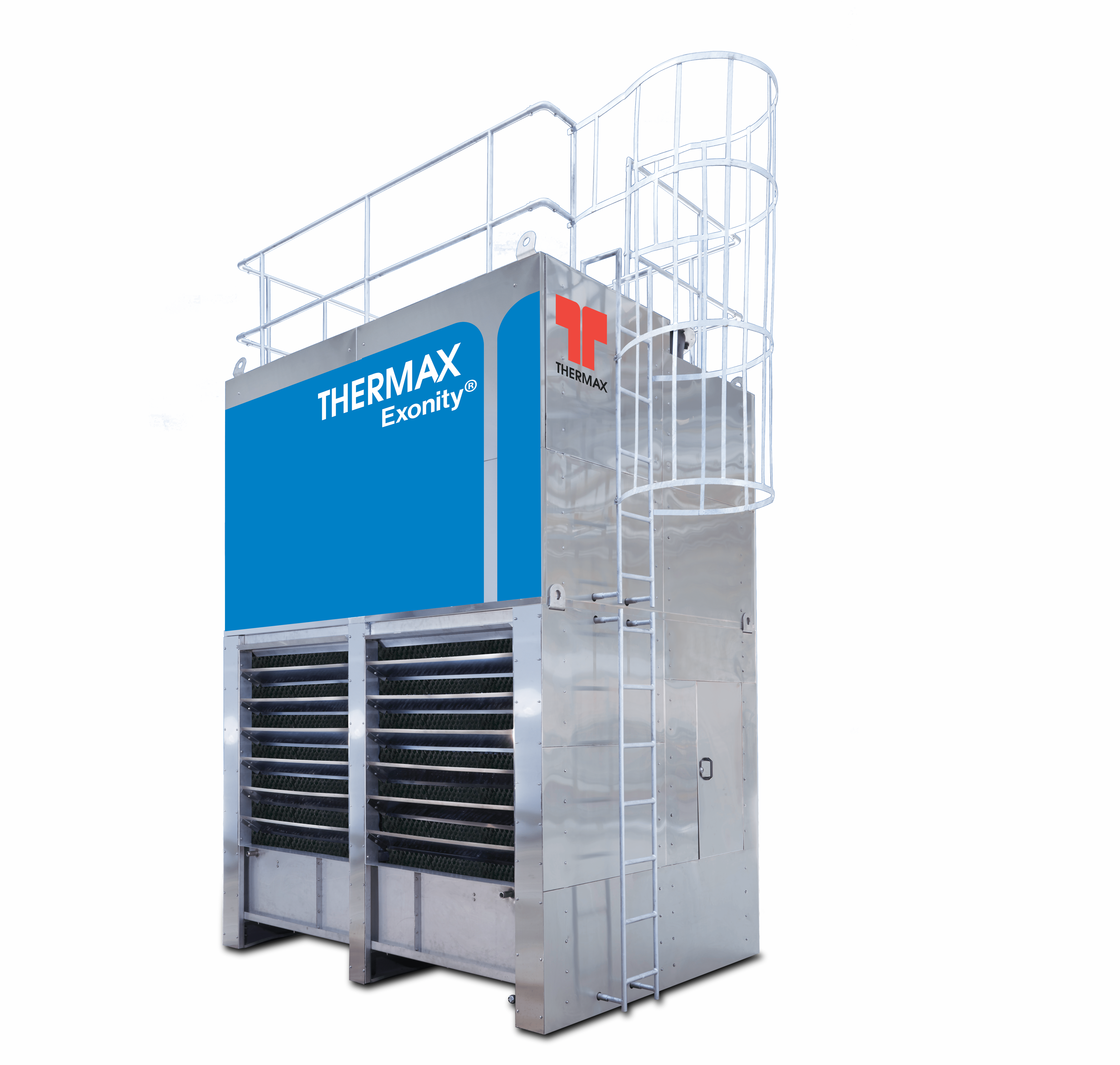
EVAPORATIVE CONDENSER
Product Features
- Replacement product against conventional systems (atmospheric condenser, shell & tube heat exchanger + cooling tower, plate heat exchanger + cooling tower)
- For ammonia/freon condensation at lower temperature
- Ideal for various refrigeration systems and climatic conditions
- Compatible with all types of refrigeration compressors i.e. reciprocating, screw, scroll, rotary and centrifugal
- Combined and counter flow technology available
- Modular construction allows plug & play installation for new and replacement units
Product Capacity: 50 TR and above
Capacity: 20 m3/h onwards
REFERENCES
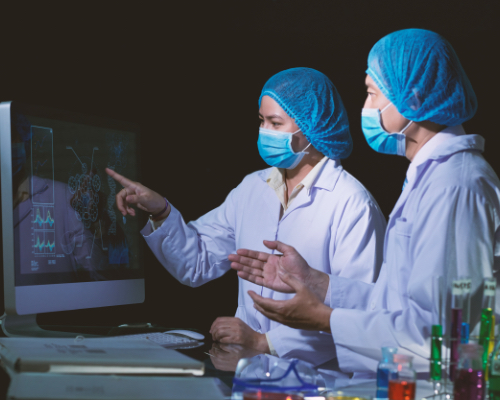
Applied Medical Research
Location: USA
Type: Low temperature hot water driven absorption chiller
Capacity: 375 TR
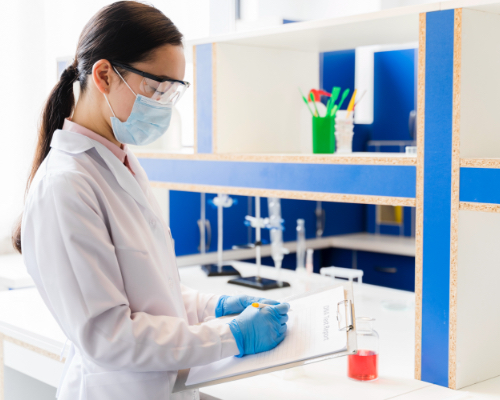
Steril Gene Life Sciences
Location: India
Type: Double effect steam fired absorption chiller
Capacity: 500 TR
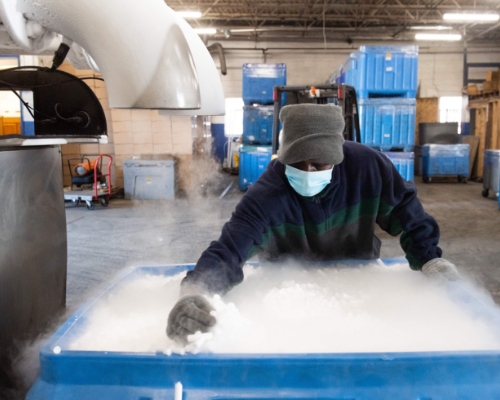
Astrazeneca Pharma India Limited
Location: India
Type: Double effect steam fired absorption chiller
Capacity: 350 TR
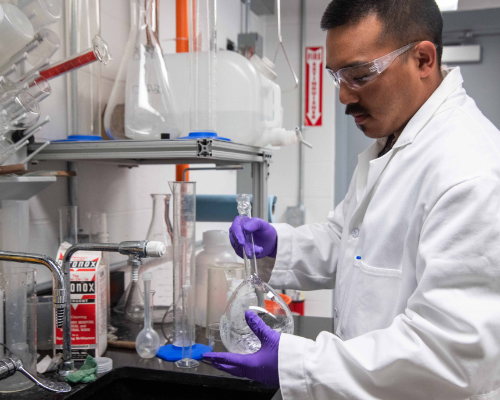
Kwality Pharmaceuticals Ltd
Location: India
Type: Double effect steam fired absorption chiller
Capacity: 310 TR
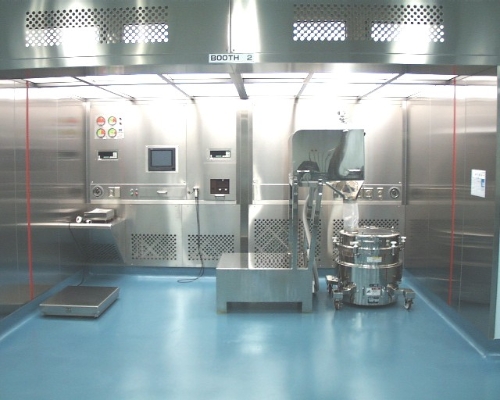
Pfizer Ltd
Location: Ireland
Type: Low temperature hot water driven absorption chiller
Capacity: 273.6 TR
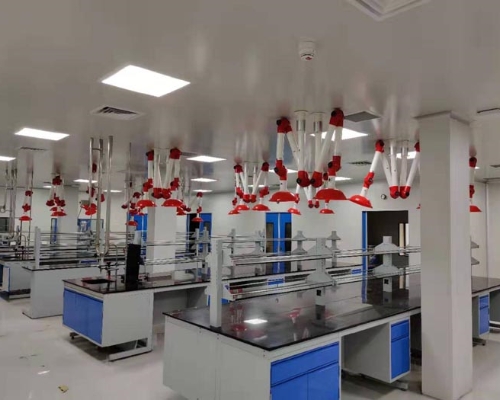
Novartis (Bangladesh) Limited
Location: Bangladesh
Type: Double effect direct fired absorption chiller
Capacity: 250 TR
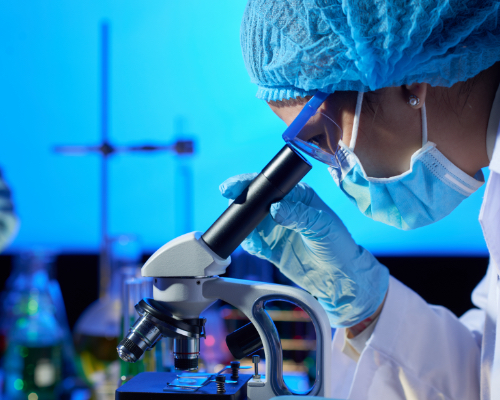
Hetero Drugs
Location: India
Type: Evaporative Condenser
Capacity: 278 TR
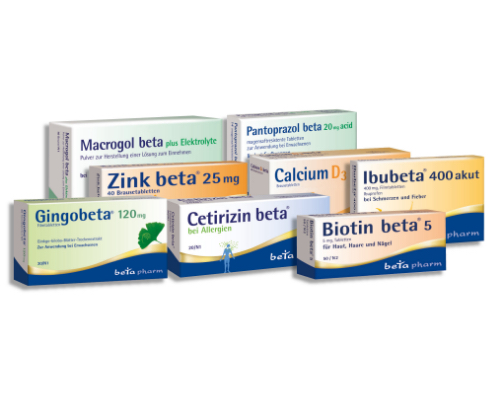
Dr Reddy’s
Location: India
Type: Evaporative Condenser
Capacity: 135 TR