- Sub Zero cooling – Thermax machines can achieve temperature of 1oC for water and a temperature as low as low as -5oC for brine, a unique feature of this technology.
- Zero crystallisation design – Online concentration measurement and control ensures that the machine doesn’t crystallise in adverse operating conditions.
- Advanced Series flow cycle – Series flow cycle ensures negligible possibility of corrosion in the machine.
- Online concentration measurements & controls – Thermax machines are provided with special concentration measurement and control system for enhanced reliability.
- Marine water boxes – The water boxes on one side of absorber and condenser is of marine type that provides easy access to tube bundle without disconnecting any piping.
- Plate heat exchangers – PHEs help to reduce the heat input required significantly as compared to conventional shell and tube heat exchangers, by increasing internal heat recovery.
- Widest tube metallurgy – Thermax VAMs tube metallurgy is customised on basis of water quality to prevent corrosion of tubes. Titanium and Stainless Steel tubes can be provided for extreme water conditions like sea water.
- Ferritic Stainless steel tubes – These have thermal expansion coefficients very close to carbon steel, due to which the thermal stresses are much lower than conventional copper tubes or copper alloys. These tubes are used in steam and hot water circuit.
- Large temperature difference in chilled water applications – Temperature difference upto 30oC is acceptable for chilled water applications.
- Minimum acceptable cooling water temperature – Thermax machines can accept cooling water temperature as low as 10oC
- Corrosion inhibitors – Thermax machines use the new generation corrosion inhibitor, Lithium molybdate, which is more effective than conventionally used Lithium nitrate and Lithium chromate. Lithium nitrate can generate Ammonium nitrate which can be harmful to the machine.
ABSORPTION COOLING
Thermax is a leading manufacturer of vapour absorption cooling systems. Thermax vapour absorption chillers are extensively used worldwide for industrial refrigeration, air conditioning, process cooling and heating. Our absorption cooling and heating business offers an extensive range of chillers that use waste steam, hot water, thermic fluid, exhaust gases and other fuels.
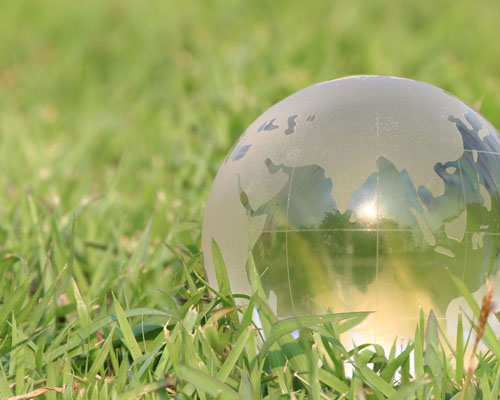
- Isolation valves in pumps for minimum downtime – Isolation valves, provided on the pumps, facilitate machine mounted pump maintenance, without breaking the vacuum. This ensures minimum downtime.
- Two stage Evaporation technology – This ensures lowest specific fuel consumption thereby resulting in lowest water consumption in cooling tower and hence saving the precious water.
- Split evaporator design – This special design feature increases the efficiency considerably.
- Gravity feed system – Thermax machines use gravity feed, non-pressurised super-spraying system, for spraying refrigerant and absorbent. This avoids the use of nozzles, which have the problems of clogging and wear & tear.
- High efficiency online purge system – Any non-condensable gas generated in the machine during operation, is purged continuously into the storage tank, thereby maintaining low vacuum in the shell and ensuring consistent performance.
- 10-100% step less modulation – For loads ranging from 10-100% of designed capacity, this machine is capable of maintaining uniform temperature of chilled water leaving the machine.
- Single exhaust driven machine on multiple engines – Heat recovery from multiple engines can be done by single machine having separate dedicated tube banks to a particular engine thereby avoiding mixing of flue gases and back pressure.
- Maximum heat recovery from exhaust gas – The exhaust gas coming from natural gas fired engine can be cooled up to 130oC and diesel fired engine can be cooled up to 180oC thereby giving maximum system efficiency.
- Auto purging – The automatic purging system eliminates the need for periodic monitoring of purge tank pressure and operation of purge system. (Optional Feature)
PLC Controls
-
- User friendly operation
- Elaborate diagnostics
- Data acquisition and logging with adjustable sampling time
- DCS/BAS/BMS connectivity via MODBUS-RTU Protocol
Safety
-
- Antifreeze protection
- Crystallisation protection
- Pump cavitation free
- Alarm cycle
- Motor protection
*Disclaimer: All the above features are general in nature and may vary from machine to machine. In view of the constant endeavour to improve the quality of products, we reserve the rights to alter or change specifications without prior notice.
- Chemical
- Beverages
- Automobile
- Dairy
- Pharmaceuticals
- Refinery
- Petrochemicals